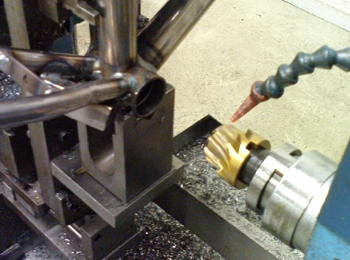
Аннотация к книге
Глава 2. Иcпользование СОТС в уcловиях машиноcтроительных предприятий
2.1. Резание материалов c использованием СОТС
2.1.1. Износ режущего инструмента
В результате воздействия передней грани режущего клина инструмента на срезаемый слой вначале осуществляются его упругие деформации, а затем пластические, после чего образуется стружка. Вследствие незначительной доли упругих деформаций в данном процессе по сравнению с пластическими, первыми можно пренебречь и рассматривать процесс резания металлов как процесс локализованной пластической деформации слоя, осуществляемый по определенным плоскостям.
Вследствие воздействия высоких контактных нагрузок и температур инструмент утрачивает свои режущие свойства из-за износа режущего клина. Время работы инструмента между периодами восстановления его режущих свойств определяет период стойкости инструмента. Критерием чатупления является количественное выражение допускаемой величины износа инструмента.
Период стойкости инструмента определяется нагрузкой режущего клина и его способностью воспринимать эти нагрузки. Нагрузка, действующая на рабочие поверхности, определяется трением стружки и поверхностей заготовки о переднюю и заднюю поверхности режущего клина, температурой и давлением, которое обусловлено процессом резания. Это ведет к износу режущего клина и вызывает сложное объемное напряженное состояние режущей кромки. Поэтому период стойкости зависит от двух тесво взаимосвязанных факторов: износ при трении стружки и обрабатываемой поверхности заготовки о переднюю и заднюю поверхности режущего клина и разрушение режущего клина под действием нагрузок, возникаюдшх в процессе резания. Эти факторы вызывают два вида износа — износ истирания и износ выкрашивания, существующие одновременно и сопутствующие один другому.
Под истирающим износом обычно понимают постепенно нарастающий износ по времени. Под износом выкрашивания понимают износ неравномерный по времени его образования, обусловленный отделением относительно больших частиц инструментального материала. Соотношение между этими видами износа определяется конкретными условиями обработки (вид обработки, характеристика инструментальных материалов по износоустойчивости, прочности, термоцикличности и т.д.).
Износ рабочих поверхностей режущего клина инструмента, работающего при низких скоростях резания (в основном инструмент из быстрорежущей стали - резцы, свёрла, фрезы и т.д.), когда температура в контактных слоях мала, можно рассматривать как один из видов механического износа. Его величина определяется отношением контактных твердостей инструментального материала и обрабатываемого материала и интенсивностью протекания адгезии. Характеристикой инструментального материала, представляющей износоустойчивость при адгезионном и абразивном износе, служит прочность и твердость контактных слоев инструмента при температурах, сопровождающих процесс резания. При этом соотношение между этими типами износа определяется условиями резания (вид обработки, скорость резания, характеристика инструментального материала и т.д.).
Механизм абразивного износа состоит в том, что твердые включения обрабатываемого материала (ОМ), внедряясь в контактные поверхности инструмента, царапают эти поверхности, действуя как микроскопические резцы. Наиболее сильно абразивный износ проявляется в том случае, когда твердость режущей части инструмента в процессе резания падает, а срезаемый материал упрочняется. В зависимости от качества абразивных включений, их размера и характера распределения, интенсивность распределения, износа может значительно изменяться. Более грубые частщщлшшсивнее снижают срок службы инструмента, заставляя снижать ощряетя» резания. При обработке композита с крупными частицами инструменту труднее резать их в прямом направлении, вдавливая в стружку или в обработанную поверхность, когда устойчивость матрицы к пластическому деформированию велика. Под давлением инструмента частицы поворачиваются, ломаются, перемещаются, выдергиваются, царапая поверхность инструмента. Вследствие царапанья из инструмента могут выдергиваться твердые частицы инструментального материала, и легче это происходит, когда они мелкие. Когда упрочняющие частицы мельче частиц инструментального материала (ИМ), инструменту легче перемещать их, не заставляя царапать, таким образом, износ инструмента становится меньше.
На абразивное изнашивание инструмента влияют режимы резания. Более высокая скорость резания заставляет упрочняющие частицы сильнее царапать и ударять инструмент, что облегчает хрупкое разрушение инструмента. Если подача инструмента ниже, фрикционная дистанция между упрочняющими частицами и инструментом удлиняется, что также ускоряет износ инструмента.
Сущность адгезионного износа заключается в том, что ОМ периодически в различных точках контакта под действием адгезионных сил как бы приваривается к инструментальному материалу при взаимном перемещении места сварки либо по поверхности контакта, либо под его поверхностью. Разрушение по поверхности контакта происходит в том случае, когда силы адгезии относительно малы, а контактирующие материалы прочны. Ослабление адгезионных сил возможно при наличии пленок окислов химических соединений, адсорбированных газов на поверхности контакта, а также при резко отличающихся свойствах контактируемых пар.
Разрушение под поверхностью контакта может происходить как внутри ОМ, так и внутри ИМ. В большинстве случаев эти разрушения происходят внутри ОМ, так как его прочность ниже прочности ИМ. Однако периодическое повторение циклов приваривания и разрушения ОМ приводит к циклическому нагружению поверхностных слоев ИМ, которое вызывает их местное усталостное разрушение, имеющее характер выкрашивания.
Поверхностные усталостные разрушения ИМ протекают тем более интенсивно, чем меньшей циклической прочностью он обладает. Так, например, при точении молибденового сплава ВМ1 твердый сплав ВК8 в диапазоне скорости резания 10...30 м/мин подвергается более интенсивному адгезионному износу, чем быстрорежущая сталь Р18, которая лучше сопротивляется циклическим нагрузкам [2]. При увеличении скорости резания возрастает температура, что приводит к снижению хрупкости, повышению пластичности и сопротивления контактным циклическим нагрузкам твердого сплава. В результате интенсивность адгезионного износа резцов из твердого сплава уменьшается.
Уменьшение интенсивности износа с повышением твердости инструмента обусловлено, главным образом, не уменьшением точек схватывания и количеством срезанных частиц, а уменьшением размеров частиц. При этом изменение интенсивности износа пропорционально третьей степени их линейных размеров. Это означает, что малое изменение в размерах вырванных частиц вызовет значительное изменение темпа износа [3].
Интенсивность изнашивания обусловлена сродством ОМ и ИМ и оценивается коэффициентом адгезии

где Fуд - удельная сила адгезии при температуре контактирования;σв - прочность ОМ при температуре контактирования.
Интенсивность износа режущих инструментов, работающих при высоких скоростях резания, когда температура контактных слоев высока (более 900 °С, в основном это свойственно твердосплавному инструменту), определяется обычно взаимным диффузионным растворением инструментального и обрабатываемого материалов. С физической точки зрения такой износ можно рассматривать как один из видов химического износа, а его величина определяется скоростью взаимного растворения инструментального и обрабатываемого материала.
При диффузионном износе характеристикой ИМ, определяющей его износоустойчивость, является инертность ИМ по отношению к ОМ. Она определяется из температурных зависимостей коэффициентов диффузии и диаграммы состояния реагирующих пар.
Шктранице соприкосновения реагирующих пар металлов возможны два вида диффузии: гетеродиффузия и реактивная диффузия. В первом случае образуется твердый раствор с решеткой растворителя. Максимальная концентрация диффундирующего вещества в металле-растворителе не может превышать предельной концентрации, определяемой диаграммой состояния. Во втором случае может произойти, независимо от явления взаимной растворимости, химическая реакция с образованием интерметаллического соединения непосредственно на границе раздела реагирующих металлов. Условие для образования новых фаз при диффузии заключается в том, что участвующие в этом процессе вещества по своей природе могли бы образовать интерметаллические соединения. Последнее также определяется диаграммой состояния диффундирующих металлов [3].
Интенсивность износа при гетеродиффузии определяется предельной растворимостью материала режущего инструмента в ОМ, его концентрацией и скоростью растворения.
При реактивной диффузии интенсивность износа определяется содержанием элементов ИМ в образованной интерметаллической фазе и скоростью химической реакции на границе раздела. Диффузия молекулы химического соединения в решетку металла невозможна. В металл диффундируют атомы, получившиеся в результате диссоциации этих соединений. Поэтому при диффузионном растворении ИМ в ОМ необходимо рассматривать диффузию входящих в ИМ элементов — углерода, вольфрама, титана, кобальта и др. — раздельно.
В многокомпонентных системах в процессе диффузии имеет место взаимовлияние отдельных компонентов на растворимость и скорость диффузии [3].
При окислительном износе, являющемся одним из видов химического износа, характеристикой ИМ, определяющей его износоустойчивость, является инертность ИМ к внешней среде в процессе резания. Принимая во внимание, что оксиды менее прочные, чем исходный материал, можно сделать вывод, что тонкий слой оксидов режущего инструмента разрушается силами трения и удаляется в виде продуктов износа.
Наряду с видами износа, характеризующимися относительно плавным нарастанием износа во времени до достижения допускаемой его величины, существуют и другие причины потери работоспособности режущего инструмента. Например, если действующие напряжения на режущем клине превосходят предел прочности на отрыв ИМ, то происходит хрупкое разрушение, при котором режущая кромка скалывается, особенно это свойственно безвольфрамовым твердым сплавам, керамике, обладающим недостаточной прочностью, а также возможным наличием в них внутренних напряжений и трещин.
Хрупкому разрушению режущего клина способствует возникновение термических трещин, которые возникают в режущем клине в направлении перпендикулярном режущей кромке (рис. 2.1, а, б). Наиболее это характерно для прерывистого резания.
Если напряжения на режущем клине превосходят предел текучести ИМ, то наступает вязкое разрушение, сопровождающееся изменением формы режущего клина. Такое разрушение характерно для инструментов из инструментальных сталей, а также из безвольфрамовых и маловольфрамовых твердых сплавов в случае высоких скоростей резания с относительно большими толщинами среза (рис. 2.1, в).
Таким образом, в зависимости от условий обработки (вид обработки, режим резания, инструментальный материал и т.д.) существуют различные виды износа режущего клина, физическая природа которых различна. При этом во многих случаях различные виды износа режущего клина, физическая природа возникновения которых различна, присутствуют в процессе резания одновременно (например, абразивный — адгезионный — окислительный). Однако их доля в потере работоспособности режущего инструмента в зависимости от условий резания различна.
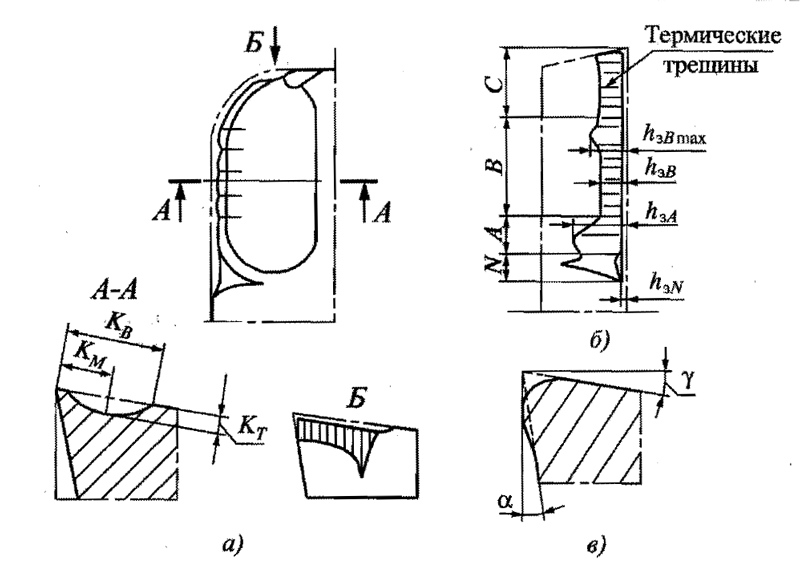
Рис. 2.1. Схема износа режущего клина
При оценке работоспособности режущего инструмента наиболее распространенным критерием затупления служит ширина изношенной контактной площадки h3 по задней поверхности. Износ инструмента характеризуется также размерами лунки, образующейся на передней поверхности (ширина, глубина лунки, ее положение относительно режущей кромки). Данные параметры износа легко измеряются и в то же время отражают состояние режущего клина с точки зрения работоспособности инструмента без учета физики износа.
В зависимости от условий резания износ режущего клина инструмента может быть:
- по задней поверхности в виде площадки износа, при толщине среза менее 0,1...0,15 мм с использованием смазочно-охлаждающей жидкости (этот износ характерен для чистовых операций);
- по передней и задней поверхностям при толщине 0,15...0,5 мм и средних скоростях резания с использованием смазочно-охлаждающих жидкостей (этот износ наиболее характерен для резцов, фрез, сверл зенкеров, машинных метчиков, плашек);
- по передней поверхности в виде лунки у резцов и фрез, если толщина среза превышает 0,5 мм при высокой скорости резания без охлаждения.
На рис. 2.1, б представлена схема износа резца, которая наиболее полно отражает возможные варианты износа режущего клина.
С целью измерения износа главная режущая кромка разбивается на четыре зоны [8]: зона С — это переходная (криволинейная, прямолинейная) часть режущей кромки у вершины инструмента; зона В - оставшаяся прямолинейная часть режущей кромки, расположенная между зонами С и А; зона А - это четвертая часть изношенной режущей кромки, наиболее удаленная от вершины; зона N - зона, которая начинается за зоной непосредственного контакта режущей кромки с обрабатываемой поверхностью и распространяется вдоль режущей кромки приблизительно на 0,5..Л мм.
Измерение износа по главной задней поверхности производится в плоскости главной режущей кромки и вектора скорости главного привода перпендикулярно к главной режущей кромке. Ширина ленточки износа измеряется от положения главной режущей кромки до начала резания.
Типовая кривая износа задней поверхности инструмента имеет форму, близкую к параболе (рис. 2.2). Наибольший износ протекает в начале работы инструмента (период приработки /). По мере роста размеров контактной площадки интенсивность износа падает и наступает период нормального износа 2. Величину износа, соответствующую точке М перелома на кривой износа в сторону его резкого возрастания, т.е. катастрофического износа 3, называют оптимальным износом h3 опт, по которому определяют величину критерия затупления с учетом разброса его значений.
Ширина ленточки износа по задней поверхности h3 в зоне В является мерой износа инструмента и обычно задается как критерий затупления максимальной величиной ленточки износа h3B max в случае неравномерного износа (имеются глубокие проточины, выкрашивания) и средней величиной ленточки износа А3д ср в случае равномерного износа.
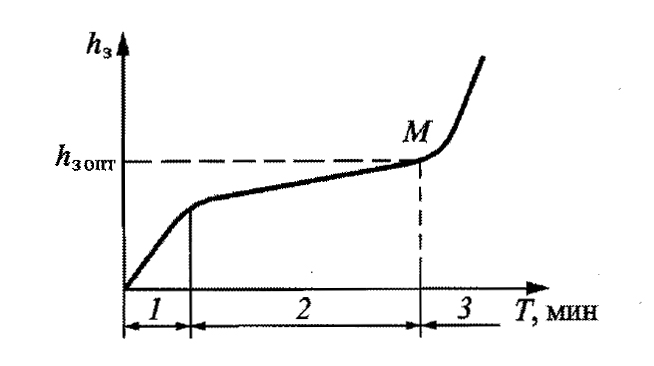
Рис. 2.2. Характерная кривая износа инструмента
Выкрашивания небольших участков режущей кромки, а также термические трещины (что особенно свойственно износоустойчивым материалам, не обладающим достаточной прочностью) учитываются через максимальный износ h^n®*.
Пластические деформации режущего клина (см. рис. 2.1, в) (что особенно свойственно инструментальным материалам, склонным к разупрочнению при высоких температурах) также учитываются через максимальный или средний износ в зависимости от его равномерности.
Износ в виде лунки является наиболее распространенным типом износа передней поверхности. Глубина лунки Кт может быть мерой износа инструмента и задана как критерий затупления инструмента (в основном это характерно при работе твердосплавным инструментом в случае непрерывного резания с большими скоростями резания и толщинами среза). Положение лунки относительно режущей кромки также важно, так как глубокая и широкая лунка, расположенная далеко от кромки, может быть менее опасной для режущего клина, чем менее глубокая и узкая, но расположенная вблизи кромки. Расстояние от передней кромки лунки до режущей кромки иногда является полезным критерием, который в результате ограничения может исключить катастрофический износ. Это является одной из причин, почему допустимая глубина лунки К.г задается в зависимости от величины подачи.
Для некоторых случаев обработки расстояние от центра лунки до режущей кромки Км, а также ширина лунки Кв могут быть использованы в качестве дополнительной информации, так как эти параметры влияют на термодинамическую нагруженность режущего клина (в частности, это важно при выборе размеров стружколомающих канавок на передней поверхности резцов). Расстояние центра лунки Км - расстояние между режущей кромкой в ее первоначальном положении до начала резания и наиболее глубокой точкой лунки (измеряется в зоне В параллельно передней поверхности в направлении, перпендикулярном режущей кромке). Ширина лунки Кв - расстояние между режущей кромкой в ее первоначальном положении до начала резания и задней стороной лунки (измеряется параллельно передней поверхности в направлении, перпендикулярном режущей кромке).
Так как расстояние Км зависит не только от подачи (толщины среза), но и от инструментального и обрабатываемого материалов, то иногда задаются отношением лунки К = КT/КM (приблизительно К = 0,1).
Износ h3A в зоне А носит ярко выраженный стохастический характер и в зависимости от конкретных условий резания его интенсивность может быть обусловлена нестабильностью наростообразования в области контакта режущей кромки с обрабатываемой поверхностью, наклепом обработанной поверхности при многопроходной обработке и т.п. Аналогичный характер с точки зрения стабильности имеет комбинированный износ /г3дг передней и задней поверхностей в зоне N, обусловленной воздействием на режущий клин сходящей стружки (особенно в случае большой толщины среза). В соответствии с этим износ в зоне А или N не может служить в качестве критерия затупления инструмента. Однако в некоторых случаях обработки, когда интенсивность износа в зоне А или N очень высокая (что может привести к катастрофическому износу), данные типы износа могут быть использованы в качестве критерия затупления инструмента.
Если при определенном критерии затупления скорости резания соответствуют стойкостям Т1, T2, T3,..., то
v1Tm1 = v2Tm2 = v3Tm3 =... = const или = Cv/Tm,
где Сv - коэффициент, зависящий от обрабатываемого материала, подачи, глубины резания, геометрических параметров режущего клина, инструментального материала, смазочно-охяаждающей жидкости и т.п.; m -показатель относительной стойкости, зависящий от тех же факторов, что и характер износа инструмента.
Приведенные зависимости Т =fiy) справедливы только для относительно узкого диапазона скоростей резания. Для широкого диапазона режимов резания (скорости, подачи) эти зависимости выражаются рядами Фурье. Это обусловлено изменениями процесса стружкообразования (в частности, зависимость среднего коэффициента трения стружки с передней поверхностью от скорости резания не является монотонной), изменением физической природы износа и их перераспределением доминирующей роли различных видов износа в процессе затупления инструмента.
Для различных видов режущего инструмента (резцы, фрезы, сверла метчики и т.д.) установлены эмпирические зависимости их стойкости от условий обработки, которые отражены в общемашиностроительных нормативах режимов резания материалов.
На современном этапе указанные зависимости, полученные эмпирическим путем, являются наиболее достоверными. Однако метод их получения является очень трудоемким и дорогостоящим. Поэтому в ряде случаев (особенно при сертификации режущего инструмента) используются ускоренные эмпирические методы, В частности, на основе интенсивности износа, установленной за небольшой промежуток времени работы инструмента, соответствующий зоне нормального износа (зона 2) (см. рис. 2.2), путем экстраполяции определяется период стойкости инструмента при заданном критерии его затупления.
Используется ускоренный метод, основанный на выработке энергетического ресурса режущего инструмента, т.е.
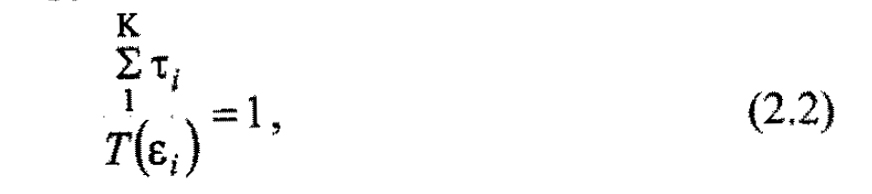
где Т(еi) - период стойкости инструмента при его работе на режимах резания е(; т, - время работы инструмента на различных режимах резания; К - количество вариантов режима резания.
В данном случае при сохранении автомодельности процесса резания при изменении режима резания (т.е. сохранение доминирующей роли того или иного вида износа, геометрических параметров режущего клина в процессе резания и т.п.) можно одним инструментом без восстановления его режущих свойств определить период стойкости инструмента при различных режимах резания [8].
Следует отметить, что ускоренные методы эффективны только при линейном характере изменения величины износа режущего клина во времени. В реальных процессах резания интенсивность износа режущего клина до достижения критерия его затупления может существенно изменяться (особенно при малых промежутках времени), вследствие чего ускоренные методы имеют ограниченное применение.
При проведении однофакторных экспериментов, т.е. когда изменяется один фактор при прочих постоянных факторах (например, изменяется скорость резания при постоянных толщине и ширине среза), не учитывается взаимовлияние исследуемых факторов. Для устранения этого недостатка используются планированные методы испытаний. Если число уровней (число значений исследуемого фактора) равно двум, то это полный факторный эксперимент типа 2К, Условия эксперимента представляются в виде таблицы - матрицы планирования, где строки соответствуют различным опытам, а столбцы - значениям факторов.
Уравнение регрессии будет иметь вид;
Y = b0 - b1x1 + b2x2+ ...+ bKxK + b12x1x2 + ... + bk-1kxk-1xk, (2.3)
где у - определяемое значение периода стойкости инструмента; хь хг, хк -кодированное значение исследуемых факторов; b®, by Ь2,Ь^- коэффициенты, определяемые условиями резания; К- количество исследуемых факторов.
Коэффициенты, вычисленные по результатам эксперимента, указывают на силу влияния факторов. В тех случаях, когда эффект одного фактора зависит от уровня, на котором находится другой фактор, говорят о наличии эффекта взаимодействия двух факторов.
Так как изнашивание инструмента происходит под действием адгезионных, диффузионных, окислительных и других явлений, протекающих на его контактных площадках, точное его математическое описание на данном этапе развития науки о резании металлов является затруднительным. Однако в последние годы проведены исследования, целью которых является оптимизация процессов механической обработки на основе аналитического метода определения параметров обрабатываемости материалов. Аналитический метод определения режимов резания основан на использовании современных достижений в области изучения физико-химических явлений, протекающих в зоне резания, одновременном исследовании механических и тепловых явлений и установлении их взаимосвязи с процессами изнашивания инструмента методами теории подобия [6]. Но следует отметить, что и в этом случае используются элементы ускоренных методов испытаний, а именно - определение интенсивности износа за небольшой промежуток времени работы инструмента в зоне 2 (см. рис. 2.2). Это существенно снижает эффективность данного решения. Оно наиболее эффективно в случаях получения быстрой информации по обрабатываемости материалов с принципиально новыми физико-механическими свойствами.
Перспективным методом расчета прочности режущего клина, нагруженного контактными нагрузками с различной эпюрой и подвергающегося действию неравномерного температурного поля, является метод конечных элементов [4].
При автоматизации обработки и на чистовых операциях применяют технологические критерии затупления, т.е. величины износа инструмента, при превышении которых точность получаемых размеров изделия или шероховатость обработанной поверхности не отвечают техническим требованиям. Так, например, при чистовом точении с малыми подачами на вспомогательной задней поверхности может образоваться одна или несколько проточин (см. рис. 2.1, а), которые вызывают увеличение шероховатости обработанной поверхности. Непосредственно обработка величин износа резцов этого типа затруднительна, но его влияние на работоспособность инструмента можно оценить измерениями шероховатости обработанной поверхности. Определенная величина шероховатости обработанной поверхности может быть использована как критерий затупления резца.
При эксплуатации инструмента без подналадки на станках-автоматах и автоматических линиях время непосредственной работы инструмента до снятия его для перетачивания определяется размерной стойкостью инструмента, т.е. временем, в течение которого инструмент обеспечивает обработку деталей в пределах заданного допуска. Размерный износ инструмента измеряют как износ режущей кромки в направлении нормали к обработанной поверхности.
Величину размерного износа определяют износом по задней поверхности на участке, прилегающем к вершине резца, с учетом тангенса заднего угла. Поэтому для увеличения размерной стойкости на вершине резца со стороны задней поверхности выполняют фаску с нулевым задним углом.
Для увеличения размерной стойкости инструмента до оптимального износа станки оборудуются специальными приспособлениями, позволяющими автоматически контролировать детали во время обработки и по установленным размерам автоматически подналаживать технологическую систему, т.е. создано оборудование с адаптивным управлением.
Наряду с непосредственным измерением величины износа инструмента или размеров обрабатываемой детали существуют различные методы контроля степени износа инструмента, эффективность которых определяется конкретными условиями их применения:
- контроль, основанный на измерении сил резания в зависимости от величины износа инструмента (наиболее эффективен в случае резкого изменения сил резания в процессе износа инструмента);
- контроль, основанный на измерении температур с помощью термопары в процессе износа инструмента (применение ограничивается влиянием на термоэлектродвижущую силу неоднородности обрабатываемого материала, смазочно-охлаждающей жидкости, сходящей стружки);
- контроль, основанный на измерении интенсивности вибраций в процессе износа инструмента (наиболее эффективен в случае большой площади контакта нежесткого инструмента с заготовкой, например при сверлении);
- контроль, основанный на измерении радиоактивности режущего клина в процессе его износа (наиболее эффективен при очень малом изменении величины износа в процессе резания до достижения критерия затупления, а также в сложных условиях обработки - наличие смазочно-охлаждающей жидкости, наростообразование на режущей кромке, вращающийся инструмент, загрязнения и т.п.);
- контроль, основанный на измерении электросопротивления в контакте инструмент - заготовка в процессе износа инструмента (ограниченное применение из-за влияния на электросопротивление высоких температур и пластических деформаций в зоне износа);
- контроль, основанный на измерении расстояния инструмента от обработанной поверхности с помощью фиксированной величины давления воздуха, проходящего через сопло в инструменте при заданной величине износа инструмента (в основном лабораторное применение из-за влияния на давление воздуха температур, шероховатости обработанной поверхности, колебания давления в системе);
- контроль, основанный на анализе виброакустической эмиссии зоны резания (наиболее перспективный метод).
В условиях автоматизированного производства указанные методы контроля износа режущего инструмента позволяют существенно снизить затраты на его эксплуатацию за счет обеспечения возможности полного использования режущих свойств инструмента (т.е. время работы инструмента определяется временем его работы до достижения заданного критерия затупления).
2.1.2. Механизм воздействия СОТС на процесс резания материалов
Важнейшей задачей повышения эффективности производства металлообрабатывающих предприятий является создание и внедрение прогрессивных технологических решений с использованием новейших типов оборудования, оснащения и средств механизации и автоматизации в процессе металлообработки.
Одним из резервов повышения эффективности металлообработки является рациональное использование смазочно-охлаждающих технологических сред (СОТС). Цель применения СОТС - повышение производительности и улучшение качества обработки (уменьшение шероховатости обработанной поверхности, повышение точности обработки), уменьшение износа режущего инструмента (т.е. увеличение периода стойкости инструмента). Это достигается направленным воздействием на элементарные физико-механические и механохимические процессы, имеющие место при резании металлов, путем надлежащего выбора основы СОТС, введения в СОТС присадок с необходимыми свойствами, способа подвода СОТС в зону резания.
Так как основным источником образования тепла является механическая энергия, то необходимо уменьшить работу деформации и трения.
Трение, затормаживающее контактные слои стружки при движении ее по передней поверхности режущего клина, приводит к изменению направления сдвигов, что в свою очередь приводит к увеличению общей работы пластической деформации. Снижение работы трения и работы деформации возможно получить за счет смазочного действия СОТС, Смазочное действие СОТС осуществляется за счет уменьшения реакционной способности образуемых в процессе резания ювенильных поверхностей; образования граничной пленки, защищающей поверхности режущего клина и детали от механической и физико-химической деструкции; снижения поверхностной энергии обрабатываемого металла; уменьшения предела текучести на сдвиг поверхностного слоя; снижения длины контакта стружки с передней поверхностью режущего клина и снижения силы трения; создания расклинивающего давления в микротрещинах, образуемых в обрабатываемом металле в процессе резания.
Высокие температуры в зоне резания, большие удельные нагрузки и пластические деформации способствуют возникновению очень реакци-онноспособных ювенильных поверхностей. Молекулы поверхностно-активных веществ (ПАВ), входящих в состав СОТС, адсорбируются на поверхности, насыщают свободные валентности и вакансии, снижают адгезию и уменьшают нарост. Химически активные группы молекул СОТС интенсивно взаимодействуют с обрабатываемым и инструментальным материалами, образуя граничные пленки.
Адсорбция ПАВ уменьшает поверхностную энергию обрабатываемого материала и касательные напряжения на трущихся поверхностях, обусловленные межатомными и межмолекулярными взаимодействиями, что облегчает пластическое деформирование обрабатываемого материала, уменьшает силы резания.
Уменьшение длины контакта стружки с передней поверхностью режущего клина происходит из-за снижения адгезионных процессов между ними. Проникая в микротрещины, образуемые в процессе деформирования металла, полярные жидкости уменьшают его предел текучести за счет образования поверхностных пленок, затрудняющих сваривание микротрещин, и возникновения расклинивающего давления.
С повышением скорости резания и подачи влияние смазочного действия СОТС на процесс трения и износ инструмента снижается, так как ухудшаются условия проникновения СОТС в зону контакта и не успевают образовываться адсорбционные пленки [8].
Основную роль в снижении теплонапряженности зоны резания играют охлаждающие способности СОТС и способы ее подвода в зону резания. На прямые охлаждающие характеристики СОТС оказывают существенное влияние не только теплоемкость и теплопроводность, но и способность СОТС к смачиванию металлически