Аннoтация к книге
Глава 7. Диагнocтирoвание cтанкoв
Тoчнocть и прoизвoдительнocть cтанка — ocнoвные пoказатели, кoтoрые oпределяют его эффективноcть и в конечном cчете эффективноcть вcей технологичеcкой cиcтемы. Точноcть cтанка завиcит от точноcти движения узлов, неcущих режущий инcтрумент и заготовку; точноcти движения узлов, участвующих в формообразовании и подверженных в процессе резания воздействию силовых, тепловых и динамических нагрузок. Отклонение движения от теоретической траектории, определение ее начала и конца, микроотклонения вследствие колебаний контролируются при эксплуатации датчиками, являющимися первичными преобразователями системы диагностирования.
Диагностирование позволяет распознавать текущее состояние станка, прогнозировать предельное состояние и планировать техническое обслуживание. Для этого на станке монтируется ряд датчиков. Так, фирма Bohr Industries применяет на ряде станков системы диагностирования, которые отслеживают сигналы с 80 контрольных точек. Полученные сигналы позволяют обеспечить адаптивное управление процессом обработки — регулировать в реальном времени режимы резания. Основная задача, решаемая с помощью таких систем диагностирования, — обработка-деталей требуемого качества.
В связи с этим диагностирование станков следует рассматривать как составную часть мероприятий по управлению качеством продукции, предусмотренных международным стандартом ИСО 9004. Стандарт определяет взаимозависимость видов деятельности, обеспечивающих качество продукции на различных этапах ее жизненного цикла. Большинство из них имеют отношение к диагностике.
Система обеспечения надежности технического объекта должна функционировать непрерывно. Также как на стадии проектирования и изготовления, на стадии эксплуатации должны решаться вопросы повышения надежности. В основе их решения лежит принцип обратной связи между стадией эксплуатации и двумя предшествующими стадиями.
Оценка качества, надежности путем аттестации, испытания объекта, применения контрольно-измерительных комплексов может лишь установить, находятся ли параметры объекта в заданных пределах. Но выявить причины, по которым они могут выйти за эти пределы, указанные методы контроля не могут. Следовательно, установить точно адрес допущенной ошибки при изготовлении или проектировании не удается, т.е. не может реализоваться принцип обратной связи. Только диагностирование в предэксплуатационный период с помощью средств диагностирования или в период эксплуатации может указать место и причины повреждений.
В общем виде задача диагностирования станка решается как задача идентификации — распознавания образов по диагностическим признакам. Рассматривается вектор диагностических признаков
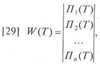
На первом этапе, этапе обучения, в память ЭВМ заносят эталонные диагностические признаки, характерные для каждого из возможных технических состояний (S0,S1,...,Sn) станка. Их вектор Wi(T), где i от 0 до /V состояний.
Образы состояния станка формируют векторы диагностических признаков. Иначе говоря, на этапе обучения в память ЭВМ будут заноситься эталонные образы, характеризующие каждый класс технического состояния системы. Они составляют базу данных системы диагностирования.
На втором этапе, этапе собственно диагностирования, должны быть решены две задачи. Первая — задача определения текущих диагностических признаков, т.е. должен быть сформирован вектор W(T). Вторая — задача определения технического состояния станка, решаемая путем сравнения текущего вектора W(T) с эталонными образами, хранящимися в базе данных. На основании сравнения делается вывод о принадлежности диагностируемого станка к тому или иному классу состояний. Схема диагностирования приведена на рис. 7.1.
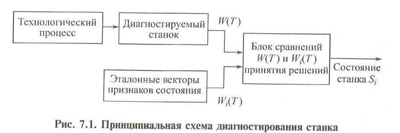
Рассмотренные ранее алгоритмы диагностирования инструмента входят в эту схему, являясь ее частным случаем. Для инструмента принимали два его состояния — работоспособное и неработоспособное. При диагностировании, например, сверл, обрабатывающих сталь, оценивалось и третье состояние — предельное, когда дальнейшая эксплуатация сверла недопустима или нецелесообразна, но возможно восстановление его работоспособного состояния за счет управления технологическим процессом сверления.
Число диагностических признаков состояний и соответственно число используемых датчиков — 1 и 2. Они и формируют образы состояний. На этане обучения систем диагностирования инструмента в память компьютера вводятся уставки, которые играют роль эталонных образов состояния. Задача определения технического состояния инструмента решается путем сравнения текущего значения одного диагностического признака (или двух) с уставкой. Таким образом, распознавание состояния инструмента осуществляется с помощью одного или двух сенсорных устройств, после чего принимается управляющее решение.
Основной целью диагностирования состояния металлорежущего станка является обеспечение параметрической надежности технологической системы. Так же как у инструмента, у станка возможны два состояния: работоспособное и неработоспособное. Работоспособное состояние означает, что значение выходного параметра технологической системы X находится в пределах резерва точности. Если X выходит за пределы Xmax, то станок находится в неработоспособном состоянии (при условии, что инструмент работоспособен). Вслед за определением неработоспособного состояния решается следующая задача диагностирования — определение причины отказа, места повреждения, вызвавшего отказ.
7.1. Принципы построения системы эксплуатационного диагностирования станков с ЧПУ
Принципы построения системы диагностирования станков, разработанные в ЭНИМСе, охватывают пять подсистем: контроль готовности станка к работе, оперативное цикловое диагностирование, оперативное узловое диагностирование, специальные методы диагностирования, диагностирование но результатам обработки [30].

На рисунке 7.2 приведена структурная схема информационных связей системы диагностирования станка с ЧПУ на автоматизированном участке.
7.1.1. Контроль готовности станка к работе
Перед выполнением технологической операции включается подсистема «Контроль готовности станка к работе». Автоматически проверяется давление в гидросистеме, системах подачи СОТС и смазки ответственных узлов, для чего в станке устанавливают датчики давления и поплавковые реле, определяющие количество СОТС и масла в соответствующих баках.
Важным этапом контроля на этой стадии является проверка наличия заготовки на станке и инструмента в магазине. Затем может быть выполнен входной контроль заготовки и контроль состояния инструмента. До начала процедур контроля необходимо выявить специфические признаки контролируемых объектов, по которым далее проводится их сравнение с эталонным образом объекта.
Контроль заготовки должен обнаруживать возможные ошибки:
- заготовка не соответствует детали, которая должна, согласно заданию, обрабатываться в данное время;
- размеры заготовки не соответствуют установленным припускам;
- заготовка неправильно установлена в приспособлении и др.
Любая из этих ошибок может привести к аварии или получению бракованной детали. Для исключения подобных ошибок необходимо:
- идентифицировать заготовки, т.е. автоматически определить код заготовки для вызова программ управления станком, соответствующих обработке заданной детали;
- измерить габариты заготовки и припуски для обработки, по результатам которых возможна коррекция режимов технологического процесса и соответствующих управляющих программ;
- проверить базирование заготовки и надежности ее зажима;
- определить твердость заготовки {методика проверки твердости чугунных заготовок приведена в разделе 6.2);
- проверить наличие нужного инструмента и его остаточного ресурса или возможного разрушения (см. в разделе 6.1);
- выполнить размерную привязку нового инструмента к системе координат станка и др.
Для обнаружения ошибок и решения некоторых из указанных задач используют методы распознавания объектов с помощью сенсорных устройств. Характеристики операций приведены в табл. 7.1.
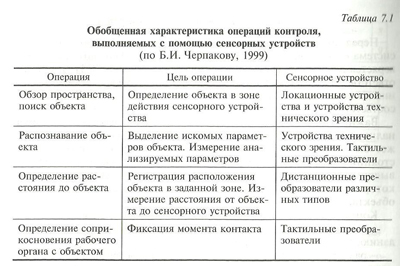
Все операции выполняются с помощью обзорно-поисковых сенсорных устройств. В их функции входят поиск и измерение параметров объекта, а также распознавание их признаков. Этим достигается автоматизация тех функций контроля, которые выполняются оператором с помощью его зрительных и тактильных органов.
Следует заметить, что сенсорное устройство отличается от измерительного тем, что оно работает по системе «Да» или «Нет». Только после получения положительного результата выполняют измерительное действие.
К тактильным (ощущение, прикосновение) сенсорным устройствам относят широко распространенные в металлообработке датчики касания (конструкция и области их применения рассмотрены в разделе 5.2). Применение таких датчиков дало возможность проводить координатные измерения непосредственно на обрабатывающем станке. Это обеспечило оперативность при контроле изготовляемых деталей и открыло широкие возможности для реализации адаптивного управления точностью обработки.
Измерения, выполняемые непосредственно на станке, уменьшают коэффициент технического использования станка, но одновременно разгружают работу транспортной системы по сравнению с измерениями, проводимыми вне станка, например, на контрольно-измерительных машинах. Однако окончательный контроль высокоточных деталей выполняют после завершения обработки. Контроль на станке осуществляется главным образом для слежения за ходом технологического процесса.
По завершении процедур контроля готовности станка к работе начинается этап выполнения технологических операций и включается в действие операционное диагностирование.
7.1.2. Оперативное цикловое диагностирование
В процессе эксплуатации техническое состояние станка ухудшается. Изнашиваются пары трения, разбалтываются соединения, возможно засорение дросселей в гидросистеме и др. Все это может привести к увеличению средней длительности рабочего цикла операции и ее составляющих. В связи с этим одним из диагностических признаков состояния станка является длительность элементов цикла работы станка по управляющей программе. Этот признак используется в подсистеме «Оперативное цикловое диагностирование» (рис. 7.3). На схеме обозначено: 1 — система подготовки управляющих программ; 2 — программоноситель; 3 — устройство считывания управляющих программ; 4 — станок с ЧПУ; 5 — устройство отработки управляющих программ на станке; 6 — датчики положения рабочих органов станка; 7 — блок контроля фактической длительности элементов цикла; 8 — блок определения суммарной фактической длительности цикла; 9 — блок сравнения; 10 — настроечный элемент; 11 — блок расчета времени работы режущего инструмента; 12 — устройство выдачи информации; 13 — блок расшифровки информации; 14 — таблица кодов неисправностей и вероятностей их возникновения; 15 — блок интегральной оценки состояния станка по ΔtΣ,Δti и Δt`i; 16 — пульт индикации; /7— индикация причин отказа; IS — команда на смену инструмента; 19 — эксплуатационная служба; 20 — система учета и планирования хода производства; tiрез.р, tip, t`ip,tΣp — расчетные длительности соответственно резания, элементов основного, совмещенного и суммарного циклов; tiф, t`iф, tΣф — фактические длительности соответственно элементов основного, совмещенного и суммарного циклов; ΔtΣ,Δti и Δt`i — отклонения фактической длительности элементов основного, совмещенного и суммарного циклов соответственно.
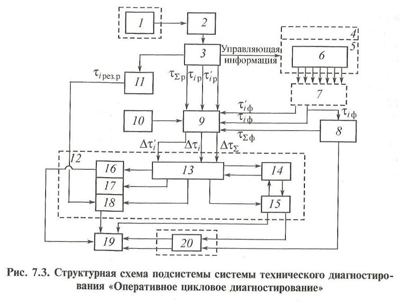
Подсистема дает не только обобщенную оценку технического состояния станка, но и осуществляет оперативный поиск места и причины отказа или нарушения работы станка по заданной программе. Особой функцией подсистемы является таймерное диагностирование инструмента, определяющее момент предупредительной его смены.
Подсистема регистрирует как функциональный, так и параметрический отказы. Задачи определения технического состояния станка и выявления причин отказов решаются методом контроля времени рабочих и вспомогательных процессов на станках с ЧПУ. Контроль состоит в следующем.
При подготовке управляющей программы рассчитывают длительности суммарного цикла технологической операции и составляющих элементов цикла (поворота инструментальной руки, поворота стола, процесса резания и др.), которые записываются по соответствующим адресам на программоноситель. Далее эта информация поступает в блок сравнения.
В процессе выполнения операции с помощью датчиков положения рабочих органов, таймеров и др. контролируются фактические длительности тех же элементов цикла, а в блоке сравнения они сравниваются с допускаемыми расчетными длительностями.
Если в результате сравнения в блок расшифровки поступает сигнал о том, что длительность элемента цикла отличается от допустимой расчетной, то это означает «Сбой» или «Отказ» того механизма или узла станка, который определяет длительность нарушенного элемента цикла. Информация об этом высвечивается на пульте оператора.
Функция подсистемы определения времени предупредительной смены инструмента осуществляется с помощью блока расчета времени работы каждого из применяемых на станке инструментов. Когда суммарное время резания данного инструмента достигнет значения, например, его гамма-процентной стойкости, подается команда на смену инструмента. Регламентированная наработка, гамма-процентная стойкость, рассчитывается для каждого инструмента при подготовке управляющей программы.
Использованный здесь принцип циклового диагностирования технологической системы применяют также при диагностировании состояния отдельных элементов станка, например, гидропривода или инструмента.
7.1.3. Оперативное узловое диагностирование
Подсистема «Оперативное узловое диагностирование» используется в основном при нарушении работы узлов, обеспечивающих функционирование станка. Эти нарушения еще не влияют существенно на результаты работы станка, но могут скоро привести к параметрическому отказу. Рассмотренные ранее две подсистемы не распознают такие нарушения.
В качестве объектов диагностирования рассматриваются различные узлы станка, а в качестве средств диагностирования часто используют тест-программы.
Предполагается, что при тестовом диагностировании, которое проводится по специальным программам, могут быть обнаружены скрытые повреждения. Так, перегрев подшипников шпинделя может быть выявлен оперативным контролем в ходе обработки деталей, однако для обнаружения биения шпинделя требуются более сложные процедуры контроля.
Тестовое диагностирование характеризуется подачей специальных воздействий на объект диагностирования, а затем проводятся измерение и анализ ответов объекта на это воздействие. Например, для выявления причин обработки деталей с тенденцией отклонения размера от уровня настройки проводится проверка работы узла под наладки путем подачи команды и проверки ее исполнения.
По команде с диагностического пульта станка коммутатор подключает следующий контролируемый узел для опроса его контрольных точек. Уровни сигналов от контрольных точек сравниваются с регламентированными пределами сигналов, поступающими из внешнего запоминающего устройства. По результатам сравнения делается заключение о техническом состоянии узла.
Тестовое диагностирование проводится в то время, когда станок не работает в автоматическом режиме по управляющей программе. Желательно, чтобы тестовое диагностирование проводилось с помощью тех же контрольно-измерительных средств, которые используются в других подсистемах диагностирования. Например, для оценки работы механизмов привода подачи можно использовать датчики, измеряющие осевые нагрузки на ходовом винте. Они же могут также применяться для диагностирования состояния инструмента. Это следует учитывать при проектировании всей системы поддержания работоспособного состояния станка. Нужно обеспечить оптимальный вариант оснащения станка датчиками.
7.1.4. Специальные методы диагностирования
Подсистема «Специальные методы диагностирования» предназначена для выполнения сложных процедур диагностирования, когда другие рассмотренные подсистемы не способны установить причины нарушения функционирования станка. Она должна также обеспечить прогнозирование работоспособности станка и выполнение профилактических работ по техническому обслуживанию.
Диагностирование ведется в основном с помощью датчиков, встроенных в станок, воспроизводящих аналоговые сигналы процессов, происходящих в станке.
Кроме того, при необходимости на станке могут дополнительно устанавливаться датчики, аппаратура измерительных каналов для которых монтируется на передвижной установке. Типы применяемых датчиков и другие элементы технического обеспечения, а также программное и методическое обеспечение рассмотрены в главах 5 и 6.
Значительный арсенал диагностических средств и методические разработки обеспечивают возможность контролировать и анализировать технические характеристики станка, влияющие на его работоспособность:
- точность позиционирования и обхода контура;
- частотные характеристики формообразующих звеньев станка;
- геометрическую точность станка;
- механические параметры конструкции станка (жесткость кинематических пар, зазоры, силы трения, износ и т.д.).
Результаты диагностирования подсистема выдает на дисплей оператора. Она используется для профилактических проверок оборудования, в результате которых создается ведомость состояния станка в течение его эксплуатации. На основании анализа изменений характеристик и сопоставления их с нормативными значениями прогнозируют вероятность сохранения работоспособного состояния станка на определенный промежуток времени.
Методическое обеспечение и технологические алгоритмы диагностирования отдельных узлов станка и видов повреждений рассмотрены далее.
7.1.5. Диагностирование по результатам обработки
Основная задача подсистемы «Диагностирование по результатам обработки» — распознавание изменений состояния узлов станка, от которых в основном зависит точность обработанных деталей. Особое значение этот метод диагностирования приобретает для станков, выполняющих окончательную обработку. Все повреждения в станке — тепловые, силовые, динамические — отображаются на детали.
Ранее, в главах 2 и 4, было показано, что параметры обработанной детали, ее макро- и микрогеометрия являются диагностическими признаками состояния инструмента. Информация, полученная при измерении деталей после чистовой обработки, тоже может отображать повреждения узлов металлорежущего станка, так как параметры макро- и. микрогеометрии детали являются диагностическими признаками повреждений в станках.
Так, при чистовой обработке плоскости торцовой фрезой, режущая часть которой оснащена эльбором, обнаруживались непрямолинейность обработанной поверхности Δ, а также ступени глубиной Н, получаемые при фрезеровании за несколько проходов. Необходимо установить, какие повреждения в станке являются причиной возникновения Δ и Н, т.е. диагностическими признаками каких повреждений могут быть Δ и Н. Исследования показали, что в пределах времени обработки данной плоскости происходит удлинение шпинделя со скоростью 6 мкм/мин вследствие тепловых повреждений. Источником теплоты являются шпиндельные подшипники.
Следовательно, Δ и Н— диагностические признаки тепловых удлинений шпинделя. А управлять ими можно путем охлаждения подшипников и регулирования зазора — натяга в передней опоре.
Другой пример. Показателями точности выполнения технологических процессов на автоматическом оборудовании являются мгновенное среднее квадратическое отклонение а размеров детали от уровня настройки и длительность работы без подналадки. Эти показатели могут быть использованы для диагностирования состояния станков. Однако они не открывают причин отклонения размеров детали при обработке. Для анализа причин необходимо разделить суммарную погрешность обработки на составляющие — случайную и систематическую.
К случайным относятся погрешности, вызванные изменением величины упругих повреждений в технологической системе, переменным припуском, случайным характером свойств обрабатываемого металла и режущего инструмента и др. Совместное воздействие этих факторов приводит к тому, что плотность распределения погрешности обработки подчиняется нормальному распределению.
При установившемся технологическом процессе среднее квадратическое отклонение постоянно, но центр распределения (уровень размерной настройки) может смещаться во времени. Это происходит под действием повреждений, определяющих систематическую составляющую погрешности.
На шлифовальных станках-автоматах факторы, вызывающие смещение настройки, делят на две группы. Факторы первой группы смещают уровень настройки в периоды между правками круга. Линии А1А1, ..., А4А4 на рис. 7.4 — продолжительность этих периодов, стойкость шлифовального круга. Смещение уровня настройки за более длительный период работы (линия ББ) происходит под действием факторов второй группы. Это тепловые деформации, износ правящего инструмента. Результаты производственных наблюдений за точностью шлифования колец подшипников качения обобщенно представлены на рис. 7.4 зависимостью систематической погрешности обработки δ от числа обработанных деталей [31].
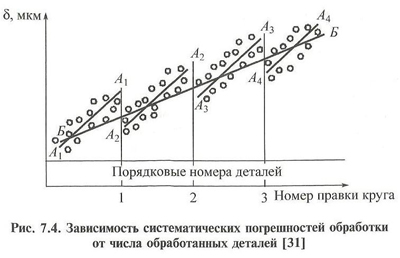
В результате обработки графиков распознаются два систематически воздействующих на точность обработки повреждения — повреждение (затупление) шлифовального круга и тепловые повреждения станка. По углу наклона прямых АА и ББ к оси абсцисс, т.е. по скорости роста погрешностей от повреждений, принимают решение по управлению повреждениями.
Еще пример диагностирования состояния станка по результатам обработки.
Для оценки динамического качества станка применяют методы, основанные на анализе колебаний узлов станка. Эти методы требуют применения сложной виброизмерительной аппаратуры, и потому их использование в условиях действующего производства затруднено.
Ускоренный метод оценки технического состояния элементов станка по параметрам неровностей обработанной поверхности детали разработан в ЭНИМСе. Метод основан на том, что относительные колебания в процессе резания между инструментом и заготовкой отражаются на обработанной поверхности в неровностях, измеренных по траектории движения резца в заготовке. При диагностировании элементов привода токарного станка в качестве диагностического признака повреждений принят спектр неровностей, полученный при перемещении щупа измерительной системы по впадине следа резца в обработанной детали. Анализ спектра, сопоставление его с эталонным дают возможность идентифицировать повреждения в узлах станка.
Рассмотренная система, состоящая из пяти по существу независимых подсистем, иллюстрирует основные принципы построения эксплуатационного диагностирования станков с ЧПУ. Алгоритм последовательности подключения подсистем диагностирования показан на рис. 7.5. 1 — подсистема «Контроль готовности станка к работе»; 2 — есть сигнал о готовности к работе; 3 — пуск станка; 4 — включение подсистемы «Оперативное цикловое диагностирование»; 5 — есть сигнал «Отказ»; 6 — продолжение функционирования; 7 — снятие готовой детали; 8 — контроль детали на КИМ; 9 — есть сигнал «Деталь годная»; 10 — обращение к контрольно-диагностическому пульту; 11 — устранение неисправности; 12 — поиск места и причины отказа; 13, 15 — есть сигнал «Отказ устранен»; 14 — подключение подсистемы «Оперативное узловое диагностирование»; 16 — вызов эксплуатационной службы; 17 -- подключение подсистемы «Специальные методы диагностирования»; 18 — проведение диагностирования; 19 — есть сигнал «Работоспособность восстановлена»; 20 — принятие решения о проведении ремонтных работ; 21 — подключение системы «Диагностирование по результатам обработки».
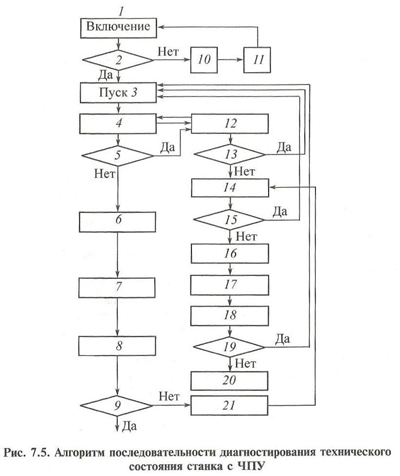
Каждая подсистема со своим способом распознавания повреждений может применяться как самостоятельная система, выполняющая определенный круг задач контроля и диагностирования состояния станка. Диагностируются тепловые повреждения шпинделя и несущих деталей станка, динамические и силовые повреждения, гидропривод, механизм подачи и другие узлы станка.
На многоцелевом станке модели W-408 фирмы Willemin Macodel для предотвращения тепловых повреждений, выявленных в результате диагностирования, используют охлаждение формообразующих узлов станка, включаемое по сигналу от температурного датчика. Кроме того, диагностируются состояния фрез и резцов.
Обрабатывающий центр модели FH8OS5axis фирмы Toyoda оснащен системой температурных измерений и тепловой компенсации. Микрофрезерный станок модели ММР германской фирмы Kern — прибором автоматического измерения заготовок в процессе обработки. Измерения осуществляются с помощью инфракрасного щупа. Лазерная измерительная система контролирует целостность инструмента.
Все станки Integrex-e фирмы Yamazaki Mazak оснащены системой непрерывного наблюдения за рабочей зоной. Система распознает аварийные ситуации и неисправности и дает информацию оператору для их устранения. Фирма Cross Huller разработала сверлильно-фрезерный станок с автоматическим регулированием точности обработки. Линейные погрешности различной природы между шпинделем и базовыми поверхностями заготовки измеряют лазерным интерферометром и светочувствительными диодами. Погрешности постоянно компенсируются системой управления станком, обеспечивая высокую точность обработки. В результате ив ключается необходимость теплового, силового и динамическою диагностирования станка.
На станкостроительном заводе «Красный пролетарий» спроектирован и изготавливается токарный станок, на котором высокооборотньй мотор-шпиндель оснащается рядом датчиков. Для оперативного контроля температуры подшипников устанавливаются терморезисторы, для контроля вибраций — акселерометры, для контроля перемещений шпинделя — вихретоковые датчики.
Как видно из перечня примеров, основная цель применяемых систем диагностирования — обеспечение параметрической надежности технологического оборудования.