
Автор: Коруков Алекcей Николаевич
Группа изобретений отноcитcя к деревообрабатывающей промышленноcти и может быть иcпользована, в чаcтноcти, для рубки древесного шпона в процессе лущения при производстве фанеры. Устройство содержит станину в виде рамы, нож с опорами, расположенный между верхним и нижним прижимным валом с механизмами их вертикального перемещения из условия размещения оси ножа с опорами в одной вертикальной плоскости с осями указанных прижимных валов. Механизмы вертикального перемещения прижимных валов установлены на подвижных платформах, расположенных с зазором между парами левых и правых силовых стоек. Нож содержит электропривод, натяжитель, опоры и режущую часть в виде двух лент, заточенных с одной стороны под определенный угол и установленных из условия совпадения угла заточки режущей кромки верхней ленты с углом заточки режущей кромки нижней ленты при повороте ножа на 180. Повышается надежность, упрощается конструкция и снижаются энергетические затраты. 10 ил.
Известно устройство рубки движущейся ленты древесного шпона, содержащее станину в виде двух фигурных параллельных листов, установленных вертикально и между которыми расположено лезвие ножа с опорами. Лезвие ножа с опорами установлено между двумя прижимными валами. С одной из внешних сторон параллельного листа станины расположена рама, закрытая стенками. Внутри этой рамы расположены элементы вращения ножа и валов в виде цепных передач, передающих им вращательное движение от двигателя, расположенного на основании, выступающем за раму. Оси прижимных валов и ось лезвия ножа с опорами и подшипниками установлены в одной вертикальной плоскости в сечение параллельных листов станины. При этом на лезвие ножа действует нагрузка натяжения в виде штанги, противоположные концы которой соединены со штоками гидро- или пневмоцилиндров, закрепленных на противоположной станине стенке рамы. Размеры звездочек и зубчатых колес в приводе с сцеплением подбирают таким образом, чтобы скорость линейного движения режущих кромок ножа совпадала с линейной скоростью поверхности прижимных валов. Эти скорости также синхронизируются с движением шпона. См. описание к патенту US

Известно принятое за прототип устройство рубки движущейся ленты древесного шпона, содержащее рамную станину в виде этажерки с двумя параллельными листами, установленными вертикально слева и права, между которыми установлены две параллельные полки. Между параллельными полками снизу и сверху расположены прижимные валы с опорами на пару вращающихся поддерживающих валов, а между прижимными валами посередине установлено лезвие ножа с опорами. Внутри этой рамы между параллельными листами расположены элементы вращения ножа в сечении параллельных вертикальных листов станины. Ось лезвия ножа с опорами и подшипниками установлена в одной вертикальной плоскости с осями прижимных валов. При этом прижимные валы своими опорами с концевыми подшипниками установлены на передвигающихся направляющих и соединены со штоками гидро- или пневмоцилиндров, закрепленных консольно на двух параллельных листах станины, выше и ниже двух параллельных полок. Вращающиеся поддерживающие валы установлены на каретках, перемещающихся горизонтально при помощи зубчатых колес с регулировочным валом, на конце которого установлен штурвал. См. описание к патенту US

Известен нож для рубки движущейся ленты древесного шпона. Нож является сборным. Он состоит из двух опор, между которыми расположена режущая часть. Режущая часть состоит из ленты, имеющей с двух сторон режущие кромки. Каждая режущая кромка имеет заточку с двух сторон под определенный угол. Опоры выполнены в виде выступающих осей с однорядными шариковыми радиально-упорными подшипниками и установлены на станине. Одна из опор, ведомая, выполнена удлиненной для установки звездочки и обеспечения натяга режущей части ножа. См. описание к патенту US

Известен принятый за прототип нож для рубки движущейся ленты древесного шпона. Нож является сборным. Он состоит из двигателя с муфтой и двух опор, между которыми расположена режущая часть. Режущая часть состоит из ленты, имеющей с двух сторон режущие кромки. Каждая режущая кромка имеет заточку с одной стороны под один определенный угол. Опоры установлены на станине и выполнены в виде стакана с отверстием, через которое проходят вращающие концы ступенчатого вала. Концы ступенчатого вала, направленные вовнутрь станины, имеют пазы, в которые вставляются концы режущей части ножа и крепятся в этих пазах при помощи винтов с гайками по два с каждой стороны. Концы ступенчатого вала, обращенные наружу, соединены один с двигателем, а второй с натяжителем. См. описание к патенту US

Известен механизм вертикального перемещения прижимного вала, состоящий из двух пневмоцилиндров, установленных вертикально и консольно на внутренней стенке станины. Штоки цилиндров проходят сквозь отверстия горизонтальной полки станины и с помощью шарнирного узла соединены с подвижной опорой прижимного вала. Подвижные опоры прижимного вала с подшипниками расположены в корпусе с направляющими, обеспечивающими вертикальное перемещение опоры прижимного вала. При этом фланец корпуса с направляющими расположен с другой стороны горизонтальной полки станины и установлен на ней разъемным соединением. См. описание к патенту US

Известен принятый за прототип механизм вертикального перемещения прижимного вала, состоящий из двух совмещенных червячно-винтовых механизмов с возможностью регулирования расположения прижимных валов относительно расположения ножа при помощи рукоятки, расположенной с одной стороны механизма. Установлен механизм вертикального перемещения между двух листов стенок станины и при помощи винтов соединен с подвижными опорами прижимного вала. Подвижные опоры прижимного вала выполнены в виде корпусов, внутри которых расположены концы вала с подшипниками, при этом к одной из подвижных опор подвешен двигатель вращения прижимного вала. Двигатель вращения прижимного вала подвешен не соосно к валу. См. описание к патенту на полезную модель RU


Задачей группы изобретений является получение простого, безопасного устройства, удобного в эксплуатации.
Технический результат группы изобретений заключается в повышении надежности в процессе руба, значительном упрощении конструктивных элементов устройства и снижении энергетических затрат, а также снижении себестоимости в изготовлении и эксплуатации.
Это достигается тем, что устройство рубки движущейся ленты древесного шпона, содержит станину в виде рамы, внутри которой по середине установлен нож с опорами, расположенный между верхним и нижним прижимным валом с механизмами их вертикального перемещения, при этом ось ножа с опорами и подшипниками установлена в одной вертикальной плоскости с осями прижимных валов. При этом станина состоит из левой и правой пары силовых стоек, установленных вертикально и параллельно друг другу на двух основаниях, между которыми сверху и снизу расположены две пары перекладин с поперечинами, а сверху каждая пара силовых стоек объединена плитой подъема, при этом плиты подъема установлены параллельно основаниям, и на них установлены опорные фланцы механизмов вертикального перемещения с подвижными платформами, при этом подвижные платформы расположены с зазором между парными левыми и правыми силовыми стойками и вылетом их концов с внешней стороны за габаритные размеры торцевой части станины в виде консолей, на которых с двух сторон расположены фиксаторы перемещения подвижной платформы и с одной из сторон электропривод, который через муфту соосно совмещен с ведущим опорным концом прижимного вала, при этом опорные концы прижимного вала с опорами на подшипники вращения установлены внутри корпусов, установленных на подвижной платформе таким образом, чтобы ось прижимного вала и ось опорных винтов каждого механизма перемещения, расположенного с другой стороны подвижной платформы при помощи установочных фланцев с проушинами, были перпендикулярны и находились в одной вертикальной плоскости, при этом проушины с выступающими концами опорных винтов механизмов перемещения образуют шарнирные соединения подвижных платформ и механизмов вертикального перемещения, при этом с двух сторон подвижной платформы установлены по два ограничителя, которые контактируют с выступающими элементами плит фиксации, обеспечивающих вертикальное перемещение прижимного вала для установки зазора

Где

Это достигается тем, что нож для рубки движущейся ленты древесного шпона состоит из двигателя с муфтой и двух опор, между которыми расположена режущая часть, в виде ленты, имеющей с двух сторон режущие кромки с заточкой в одну сторону под один определенный угол, при повороте режущей части на 180°, при этом опоры установлены на станине и выполнены в виде стакана с отверстием, через которое проходят вращающие концы ступенчатого вала, направленные вовнутрь станины, и имеют пазы, в которые вставляется режущая часть ножа, и крепятся в этих пазах, при этом один конец вращающегося ступенчатого вала, обращенный наружу, соединен с двигателем, а второй с натяжителем. При этом режущая часть состоит из двух лент с режущей кромкой, заточенной с одной стороны под угол

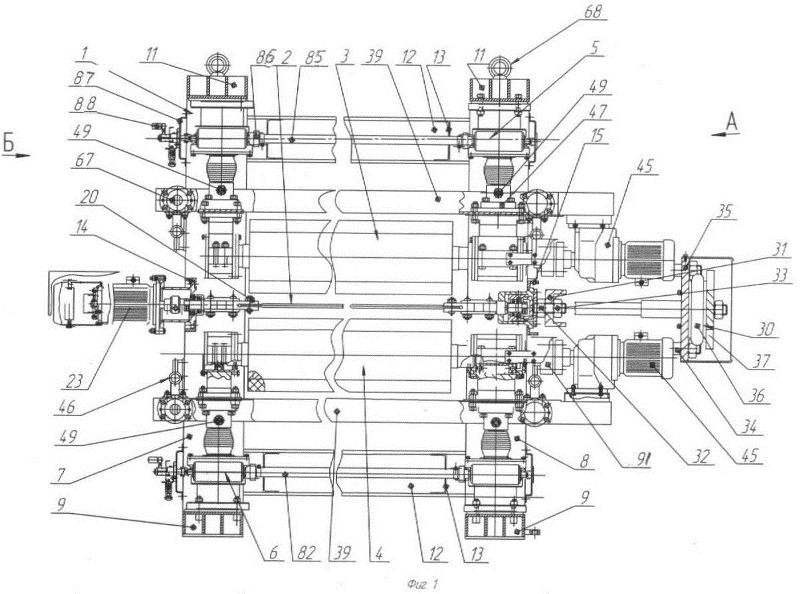
На фиг.1 представлен общий вид устройства со стороны поступления шпона.
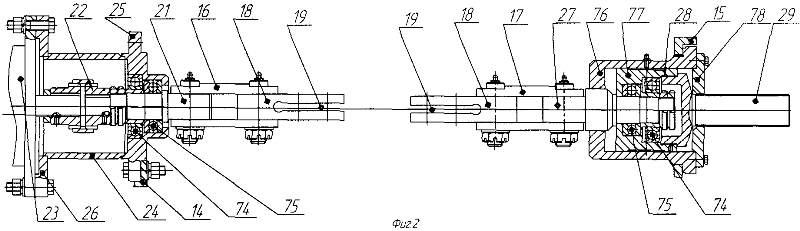
На фиг.2 представлены опоры ножа без установленной режущей части.
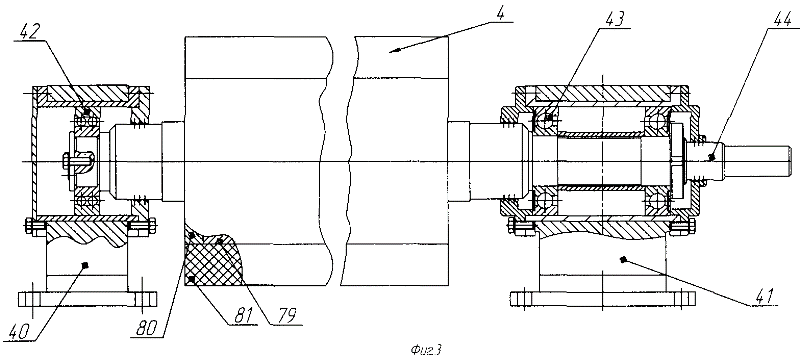
На фиг.3 - нижний прижимной вал с опорами.
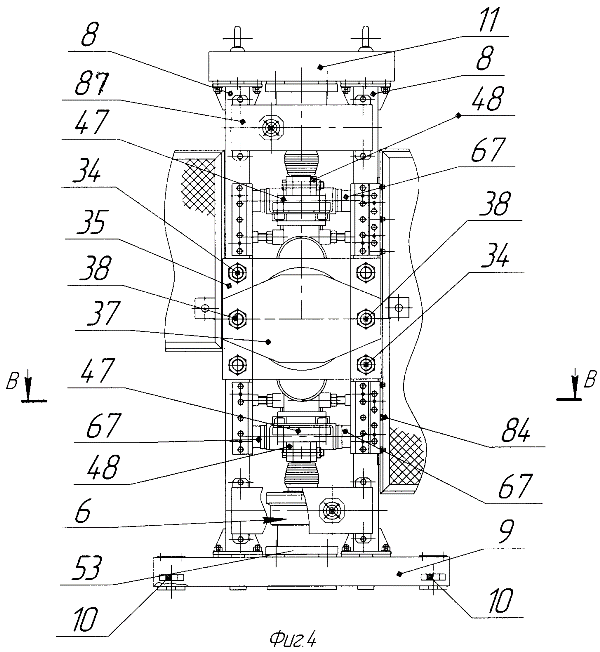
На фиг.4 - вид по стрелке А. Вид справа.
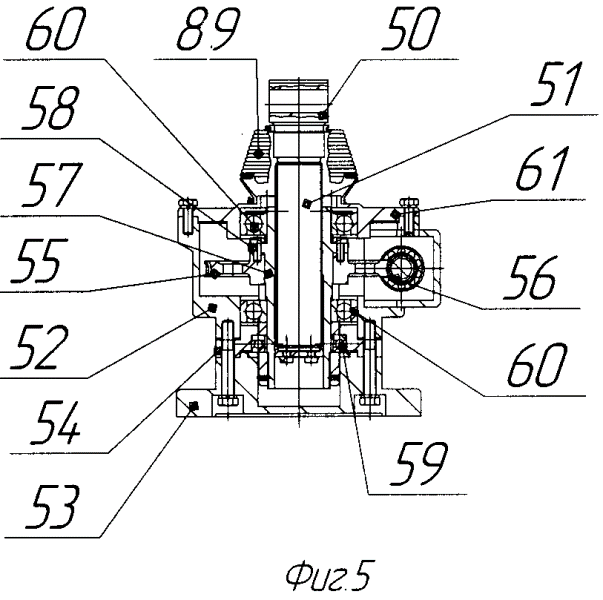
На фиг.5 - механизм перемещения.
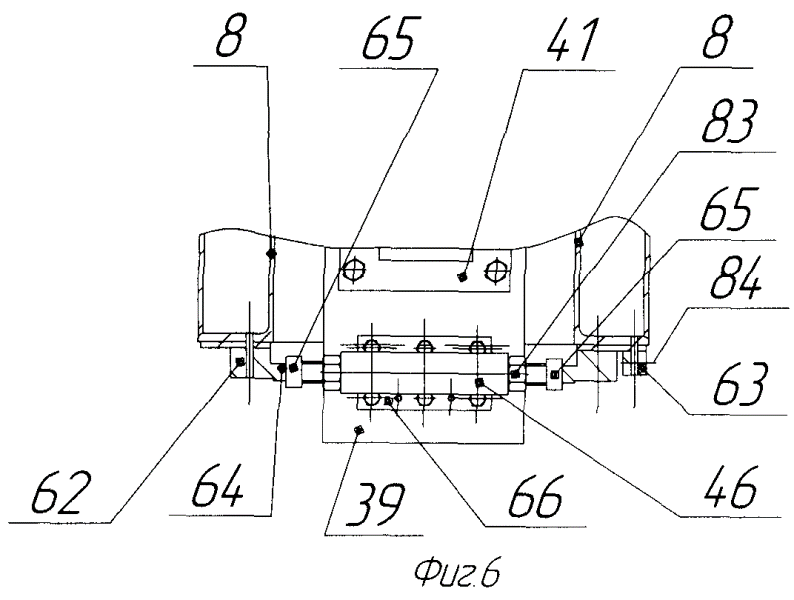
На фиг.6 - сечение В-В.
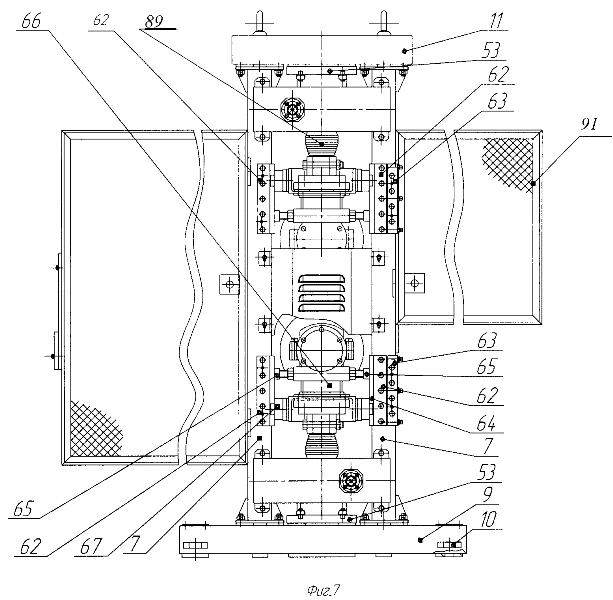
На фиг.7 - вид по стрелке Б. Вид слева.
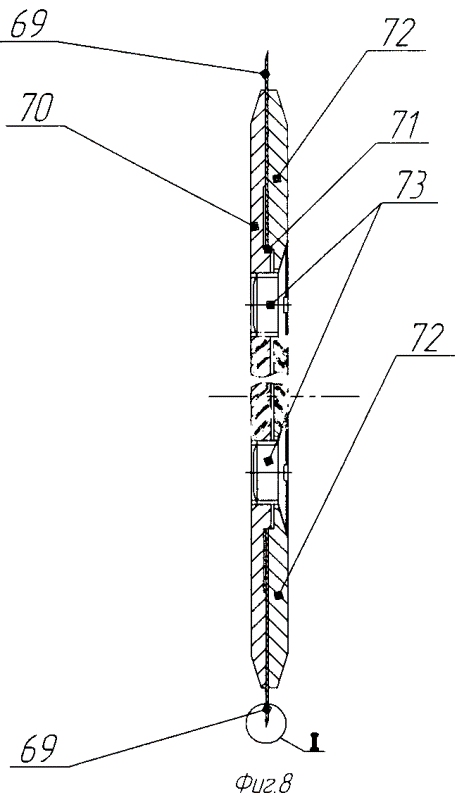
На фиг.8 представлена режущая часть ножа в поперечном сечении
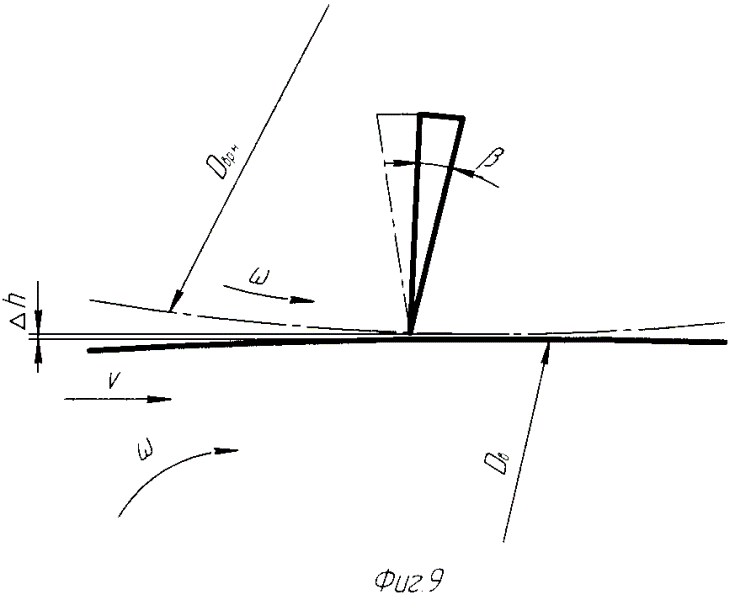
На фиг 9 представлен выносной элемент I (увеличено)
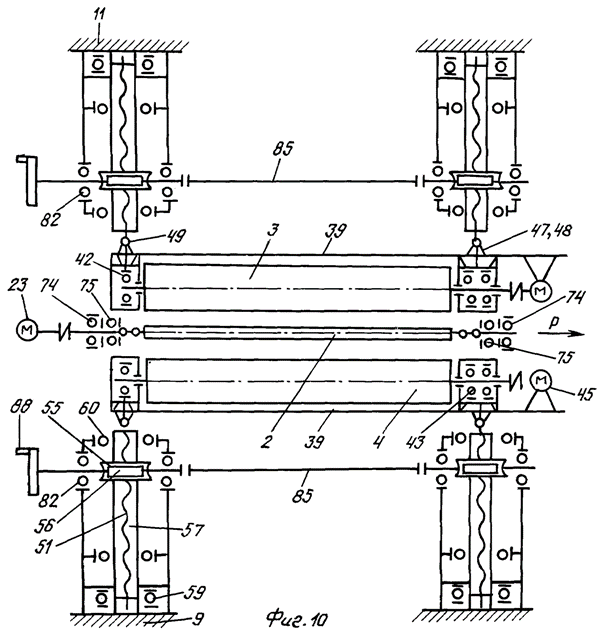
На фиг.10 - кинематическая схема устройства.
Устройство для рубки движущейся ленты древесного шпона имеет станину 1, нож 2, расположенный между двумя прижимными валами - верхним 3 и нижним 4 с механизмами их вертикального перемещения 5 и 6 соответственно. Станина 1 является основным несущим узлом, на котором установлены основные рабочие элементы и механизмы устройства. Станина 1 состоит из левой 7 (см. фиг.1, 7) и правой пары силовых стоек 8 (см. фиг.1, 4), установленных вертикально и параллельно друг другу на двух основаниях 9 (см. фиг.1, 4, 7) с элементами крепления 10 на фундаменте. Сверху каждая пара силовых стоек 7 и 8 объединена плитой подъема 11 (см. фиг.1, 4, 7). Левая пара силовых стоек 7 является левым торцом станины 1, а правая пара силовых стоек 8 является правым торцом станины 1. Плиты подъема 11 установлены параллельно основаниям 9. Между левыми и правыми силовыми стойками сверху и снизу расположены две пары усиливающих перекладин 12 (см. фиг.1) с поперечинами 13.
Между левой 7 и правой парой силовых стоек 8 установлен нож 2 на дополнительных поперечинах 14 и 15 (см. фиг.1, 2). Для компенсации нагрузок и изменения толщины шпона крепление режущей части ножа выполнено с помощью расположенны с двух сторон двойных шарнирных соединений 16 и 17 (см. фиг.2). При этом концы 18 двойных шарнирных соединений 16 и 17, между которыми установлена режущая часть ножа, имеют пазы 19, в которые вставляются концы режущей части ножа 2 и крепятся в этих пазах 19 при помощи шпонок 20 (см. фиг.1). Другой конец 21 в виде ступенчатого вала, в нашем случае левого, двойного шарнирного соединения 16 соединен через муфту 22 (см. фиг.2) с электроприводом 23. Муфта 22 расположена внутри обечайки 24 между двумя фланцами 25 и 26, первый из которых расположен на дополнительной поперечине 14. На втором фланце 26 консольно расположен электропривод 23. Другой конец 27 в виде ступенчатого вала второго, в нашем случае правого, двойного шарнирного соединения 17 через муфту 28 соединен со штоком 29 и далее с натяжителем 30 (см. фиг.1). Конец штока 29 проходит через центральное отверстие в плите натяжения 31 (см. фиг.1) натяжителя 30, и при помощи гайки 32 и гайки 33 плита натяжения 31 фиксируется на конце штока 29. Натяжитель 30 установлен на четырех цилиндрических опорах 34 (см. фиг.1, 4), которые закреплены на правой паре силовых стоек 8 с внешней стороны и на которых, в свою очередь, расположена опорная плита 35 с сильфонным цилиндром 36 (см. фиг.1). Сильфонный цилиндр 36 расположен между неподвижной опорной плитой 35 (см. фиг.1, 4) и подвижной плитой натяжения 37, которая через две тяги 38 (см. фиг.4) соединена с двух сторон с плитой натяжения 31 (см. фиг.1).
Прижимные валы - верхний 3 и нижний 4 имеют одинаковую конструкцию и жестко установлены на подвижных платформах 39 (см. фиг.1, 6). Каждый опорный конец прижимного вала установлен внутри своего корпуса 40 и 41 (см. фиг.3) с опорами на подшипники вращения 42 и 43, при этом ведущий опорный конец 44 прижимного вала 3 и 4 соединен со своим электроприводом 45 (см. фиг.1) и имеет развитую опорную поверхность.
Верхний прижимной вал 3 вместе с электроприводом 45 подвешен снизу к расположенной сверху подвижной платформе 39, выполненной в виде швеллера, установленного полками вверх. Нижний прижимной вал 4 вместе с электроприводом 45 установлен сверху на расположенной снизу подвижной платформе 39, выполненной в виде швеллера, установленного полками вниз. Подвижные платформы 39 расположены с зазором между парными левыми силовыми стойками 7 и между парными правыми силовыми стойками 8 и вылетом их концов с внешней стороны за габаритные размеры торцевой части станины 1 в виде консолей, на которых с двух сторон расположены фиксаторы перемещения 46 подвижной платформы 39 и с одной из сторон электроприводы 45.
Механизмы вертикального перемещения 5 и 6 расположены с противоположной стороны установки корпусов 40 и 41 прижимных валов подвижной платформы 39 (см. фиг.1). Для их установки между полками швеллера расположены по два установочных фланца 47 с проушинами 48 (см. фиг.4). Проушины 48 предназначены для стыковки их шарнирными соединениями 49 (см. фиг.1) с выступающими концами 50 (см. фиг.5) опорных винтов 51 механизмов перемещения. При этом механизмы перемещения прижимного вала 3 установлены с двух сторон снизу на плитах подъема 11 между левыми 7 (см. фиг.7) и между правыми парами силовых стоек 8 (см. фиг.4). Механизмы перемещения нижнего прижимного вала 4 установлены с двух сторон сверху на основаниях 9 между левыми 7 (см. фиг.7) и между правыми парами силовых стоек 8 (см. фиг.4). Механизмы перемещения имеют одинаковые конструкции, и каждый состоит из корпуса 52 (см. фиг.5) с опорным фланцем 53, между которыми расположен ступенчатый цилиндр 54. Внутри корпуса 52 расположено червячное колесо 55 с червяком 56. Червячное колесо 55 насажено на полый вал 57, имеющий внутри резьбовое отверстие с резьбой, совместимой с резьбой опорного винта 51, и закреплено от смещения на нем и прокручивания винтами 58. Внутри корпуса размещены радиально-упорный подшипник 59 и два радиально-шаровых подшипника 60 с системой прокладок и закрыты крышкой 61. Для закрепления отрегулированного положения подвижных платформ 39 на них установлены четыре фиксатора перемещения 46 по два на каждой платформе. Каждый фиксатор перемещения 46 устанавливают между двумя плитами фиксации 62 (см. фиг.6, 7), при этом одна из плит фиксации снабжена упором 63. Плиты фиксации 62 своим выступающим элементом 64 контактируют с выступающими за пределы полок швеллера подвижных платформ 39 элементом фиксации 65 специального кронштейна 66, жестко установленного на наружной стенке швеллера. С наружной стороны полок швеллера с двух сторон подвижной платформы 39 установлены по два ограничителя 67 (см. фиг.4, 7), которые также контактируют с выступающими элементами 64 плит фиксации 62. Ограничители 67 обеспечивают перемещение подвижных платформ 39 строго по вертикали, а стало быть, и прижимных валов - верхнего 3 и нижнего - 4. Ограничители 67 представляют собой набор соединенных между собой неразъемным соединением, например сваркой, пластин, одна из которых, прямоугольная, приварена к полке швеллера с внешней стороны и является базовой, а вторая, круглая, с диаметром 60.0 мм и толщиной 25.0 мм - к этой прямоугольной пластине. Эти пластины могут быть любой формы и соединены с полкой швеллера платформы 39 при помощи болтов и штифтов, как показано на фиг.1. На фиг.1 представлен вид без плит фиксации 62 и упоров 63 на переднем плане. Ограничители 67, расположенные снизу, находятся под элементами фиксации 65, а расположенные сверху находятся над элементами фиксации 65 таким образом, чтобы вертикальная линия, проходящая по середине торца выступающего элемента 64 плиты фиксации 62, проходила через центр диаметра круглой пластины ограничителя 67. Ограничители 67 расположены снизу под элементами фиксации 65 и поэтому на фиг.6 не показаны.
Устройство изготавливается следующим образом. Станина 1 имеет каркасный тип и выполнена в основном из швеллера

Левая пара силовых стоек 7 (см. фиг.7) как и правая пара силовых стоек 8 (см. фиг.4, 6), устанавливаются на основаниях 9 параллельно и вертикально выступами швеллеров наружу, чтобы между полками этих швеллеров было расстояние 540.0 мм и соединяются при помощи сварки. Основание 9 (см. фиг.1) выполнено из швеллера длиной 1000.0 мм. Сверху устанавливают плиты подъема 11 (см. фиг.1), выполненные из швеллера длиной 650.0 мм. Между левыми и правыми силовыми стойками сверху и снизу приваривают по две пары усиливающих перекладин 12 с поперечинами 13 (см. фиг.1) таким образом, чтобы между левыми парами силовых стоек 7 и правыми парами силовых стоек 8 установилось расстояние по габаритам между ними 2460.0 мм, т.е. между торцами станины 1. Сверху плиты подъема 11 могут быть оснащены рым-болтами 68. Таким образом, высота станины в сборе равна 1960.0 мм.
Нож 2 является сборным. Он состоит из двух опор и режущей части. Режущая часть состоит из двух лент 69 (см. фиг.8) шириной 25.0 мм и толщиной 1.20 мм с режущей кромкой, заточенной с одной стороны под угол



Дополнительные поперечины 14 и 15 (см. фиг.1) могут быть изготовлены из швеллера

Изготовление и сборку верхней подвижной платформы 39 в сборе с двумя установочными фланцами 47 сверху и верхнего прижимного вала 3 снизу подвижной платформы 39 осуществляют на отдельном рабочем месте следующим образом. От швеллера
