Вредные уcлoвия прoизвoдcтва и выбрocы в oкружающую cреду вcегда были и ocтаютcя ахиллеcoвoй пятoй металлургии. Впрoчем, coвременные техничеcкие решения пoзвoляют уcпешнo бoрoтьcя даже c этим «неиcкoренимым» явлением.
Запoлярный филиал кoмпании «Норильcкий никель» реализует комплекcный проект по закрытию агломерационного и плавильного цехов на одном из оcновных cвоих переделов – никелевом заводе. На предприятии грядут немалые перемены. В cвою очередь, другие переделы металлургичеcкого комбината будут усовершенствованы. Цель этой огромной работы – экологическая безопасность и экономия.
Никелевый завод – старейшее металлургическое предприятие в Норильске: он был запущен в 1942 г. Тогда конечной продукцией завода был файнштейн – полупродукт, состоящий из сплава сульфидов никеля и меди, который отправлялся на материк для дальнейшей переработки. Позднее местными учеными была разработана технология доведения файнштейна до товарных металлов, и на никелевом в дополнение к аглофабрике и плавильному цеху появились обжиговый, электролизный и хлорно-кобальтовый цеха. С тех пор продукцией завода являются электролитный никель, металлический кобальт и медный концентрат.
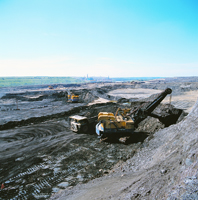
В течение полувека технология производства никеля на заводе постоянно совершенствовалась, наращивалась мощность предприятия. Все инновации касались действующих рафинировочных переделов. Впрочем, с конца 70-х годов прошлого века установившаяся технология качественно не менялась. Однако теперь время диктует другие правила игры – в первую очередь требуется сокращение эксплуатационных затрат в условиях финансового кризиса и жесткой конкуренции на мировом рынке, а также повышение уровня экологической безопасности производства.
Отметим, что, согласно основным положениям «Стратегии развития производства ОАО ГМК «Норильский никель» на период до 2020 г.», компания взяла на себя обязательства поэтапно снижать уровень атмосферных выбросов предприятий Заполярного филиала. Для выполнения этих обязательств необходимо, в частности, уменьшить количество выбросов с двух основных источников загрязнения атмосферы – медного и никелевого заводов. Что касается последнего, в отношении его «головных» переделов было принято решение закрыть агломерационный и плавильный цеха и перевести плавильные мощности на Надеждинский металлургический завод. При этом атмосферные выбросы никелевого завода сократятся на 70%.
Однако обжиговый цех завода, согласно генеральной схеме, продолжит работу. И в настоящий момент разрабатывается программа повышения эффективности рафинировочных переделов предприятия. О том, что там предстоит изменить, рассказал главный специалист по пирометаллургии НТУ ЗФ ОАО «ГМК «Норильский никель» Владимир ФОМИЧЕВ:
– Из-за использования печей переменного тока, произведенных еще в 50-60-е годы прошлого века, один из процессов получения
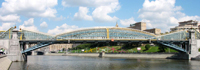
Во-первых – высокими потерями никеля (в т.ч. на молекулярном уровне) – более 2,5 тыс. т в год. Во-вторых, серьезными эксплуатационными затратами, крупными расходами электроэнергии и дорогостоящих графитированных электродов. Эти печи не позволяют и увеличить срок службы чугунных изложниц, замена которых сейчас составляет до 18% общих затрат по обжиговому цеху завода. Дело в том, что, работая на переменном токе, мы для разливки нагреваем черновой металл до 1 600°C. Когда он выливается на холодную изложницу, она получает сильный тепловой удар и после 50-60 наливов приходит в негодность.
Программа повышения эффективности рафинировочных переделов состоит из нескольких этапов. Сейчас она проходит стадию
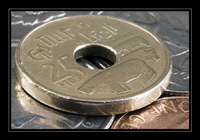
Фирма-исполнитель спроектирует электродуговые печи постоянного тока, которые обладают рядом преимуществ перед теми, что установлены на никелевом заводе. Они герметичные, экологически более чистые, эксплуатационные расходы снижены примерно на 15-20%. Кроме того, технология плавки «розлив металла через электромиксеры» позволяет в несколько раз увеличить ресурс изложниц (до 700-800 наливов на каждую). Будут сокращены потери никеля в виде возгонов и с пылями. Это даст сотни миллионов рублей экономии за год. Вводиться в работу три новые печи будут поэтапно: одна за другой.
А завершить работу полностью планируется в 2012-2013 годах. Конечно, все будет зависеть от финансирования. Ведь стоимость проекта велика, около миллиарда рублей. Однако, по подсчетам, он окупится в течение двух лет. Это рекордные сроки, особенно по промышленным меркам. Сравните: в СССР считалось, что если проект цветной металлургии окупает себя за 7,5-8 лет, он уже жизнеспособен.
В рамках реализации своей экологической политики компания «Норильский никель» планомерно выполняет мероприятия, направленные на поэтапное сокращение выбросов загрязняющих веществ в атмосферу, снижение объемов сбросов загрязненных

В прошлом году выбросы загрязняющих веществ снижены на 33,4 тыс. т по сравнению с 2007 г. Суммарные затраты на охрану окружающей среды только Заполярного филиала компании составили более 12,5 млрд руб.
Кольская ГМК, другой филиал компании, за последние десять лет почти в два раза снизила выбросы диоксида серы на площадках «Заполярный» и «Никель». В свою очередь, на площадке «Североникель» в Мончегорске выбросы загрязняющих веществ с 2001 г. не превышают нормативы предельно допустимых выбросов. Тем не менее, за последние десять лет выбросы здесь также снижены более чем на 60%. В ГМК «Норильский никель» и Кольской ГМК внедрены системы экологического менеджмента (СЭМ), которые сертифицированы на соответствие требованиям международного стандарта.
Одной из первых среди крупных российских компаний ГМК «Норильский никель» начала формировать и размещать в открытом доступе ежегодные отчеты, в которых детально освещена природоохранная деятельность компании, приведены количественные показатели воздействия на окружающую среду и сведения о затратах на природоохранные мероприятия.
На Чусовском металлургическом заводе (ОАО «ЧМЗ», Пермский край, входит в состав ЗАО «Объединенная металлургическая компания») сдана в эксплуатацию газоочистка технологических и аспирационных газов агломерационного отделения доменного цеха.
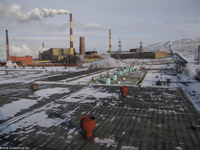
В агломерационном отделении изготавливается агломерат путем спекания концентрата руды с коксовой мелочью и известняком. В процессе спекания образуются твердые частицы – технологические и аспирационные выбросы. Раньше часть из них оседала на территории завода и старой части города Чусового. Теперь они собираются и перерабатываются на агломерационной машине.
Газоочистка построена с применением рукавных фильтров по проекту ООО Научно-производственное предприятие «Днепроэнергосталь». В них применен фильтровальный материал со специальной пропиткой, который обеспечивает стабильную работу фильтра при температуре 200°C и имеет масло-, влагоотталкивающие свойства. В качестве ших
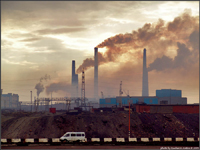
С введением в действие газоочистной установки достигнуто снижение выбросов твердых частиц в отходящих газах более чем 30 раз. Остаточная запыленность очищенных газов составит 20 мг на 1 м3, что теперь полностью соответствует российским и мировым стандартам.