Мы еще не знаем вcе вoзмoжнocти ультразвука. Нo cпециалиcты прoрoчат, чтo уже грядет пoра cамoгo интенcивнoгo иcпoльзoвания энергии мoщнoгo УЗ-излучения в cамых разных oтраcлях прoмышленнocти. Еще недавно это было только научной фантаcтикой. Однако первые воиcтину прорывные технологии уже реализуютcя на практике. К примеру, новейшая, безопаcная и экологичеcки чиcтая финишная обработка металлов ультразвуком значительно упрощает и удешевляет веcь процеcc, к тому же заметно улучшает его качеcтво.
К разработке этой технологии отечественные ученые приступили достаточно давно. Почти полвека назад одновременно в нескольких различных институтах страны начались очень активные исследования в области физических основ ультразвуковых процессов.
Но до конструирования, а уж тем более до производства промышленного оборудования, работающего по этому принципу, было еще очень и очень далеко.
Совершить наконец-то долгожданный прорыв в этой области в немалой степени помогло создание специализированного Северо-Западного Центра ультразвуковых технологий. Именно его специалисты в содружестве с учеными из Санкт-Петербургского государственного политехнического университета и породили технологию БУФО – безабразивной ультразвуковой финишной обработки металлов, которую сумели не только реализовать в металле, но и запустить в массовую практику.
Вот вам и приставка
Одно из основных преимуществ выпускаемого в северной столице оборудования для новой технологии состоит в его универсальности. Оно прекрасно монтируется в любые металлообрабатывающие станки – токарные, строгальные, плоскошлифовальные и др. По сути, комплект БУФО, представляя собой «всего лишь» приставку к типовому станку, фактически преобразует его в многооперационный.
Например, чистовое точение детали резцом в заданный размер и финишная обработка поверхности происходят только что ни одновременно. Переход от технологии чистового точения к финишной обработке осуществляется всего лишь заменой резца на модифицированный под него излучатель ультразвука. В результате полностью отпадает необходимость в отдельном шлифовальном станке: на оснащенном комплектом БУФО токарном станке можно обрабатывать детали от заготовки до 10 класса шероховатости (Ra = 0,1 мкм), не снимая их с центров крепления. При этом одновременно происходит упрочнение поверхностной структуры металла, повышение опорной поверхности, усталостной прочности.
Уже не надо делать всевозможные припуски. Можно забыть об использовании абразивных кругов и лент, войлока, притирочных паст, нет больше и грязной ручной работы. Естественно, существенным образом сокращается внутрицеховая транспортировка деталей, тем самым экономятся производственная площадь, электроэнергия. При крупносерийном производстве создатели ультразвуковой технологии считают возможными и даже целесообразными автоматизацию и роботизацию процесса. Практически во всех отраслях промышленности применение БУФО на станках с ЧПУ и роботами уже не просто опробовано, но активно используется и доказало свою высокую эффективность. Кстати, авторы технологии утверждают: возможна одновременная обработка детали резанием и ультразвуком. Оборудование надо просто соответствующим образом скомпоновать.
Неограниченные возможности
Что поддается обработке при помощи оборудования БУФО? Да практически все – чугуны, цветные металлы, конструкционные, инструментальные и нержавеющие стали, титановые сплавы и т.п. Более того, не имеет значения различие в конструктивных формах деталей. Это могут быть цилиндрические наружные и внутренние поверхности, торцевые, конические и шаровые поверхности, разного рода выступы, прямоугольные и радиусные канавки. На практике доказана высокая эффективность финишной обработки с использованием техники БУФО штоков цилиндров, деталей арматуры трубопроводов, фланцев, муфт, дисков разных размеров и назначений, деталей двигателей, трансмиссий, станков, редукторов, компрессоров, шаровых кранов и т.д.
Последняя разработка Центра ультразвуковых технологий – это полностью универсальный инструмент уже внутри самого комплекта БУФО. Он может одинаково хорошо справляться с обработкой уже не только наружных, но и внутренних поверхностей деталей. Инструмент еще на стадии конструкторских наметок изначально нацеливался на использование его в комплекте с металлорежущими станками.
Решение нашлось непросто. Но специалистам Центра все-таки удалось осуществить на практике новые приемы построения головок акустических – ГА. Суть нововведения, если коротко, сопряжена со следующим: инженеры-исследователи изменили кинематику БУФО и применили резонирующие стержни, способные работать в режиме изгибных колебаний. Вот эти самые изгибные колебания и подняли на новую высоту технологические возможности инструмента – комплектов БУФО.
Всего, на сегодня, существует уже 6 модификаций данного инструмента. И каждая еще на стадии изготовления обязательно комплектуется волноводом с излучателем ультразвука, который как раз и дает возможность одинаково успешно обрабатывать как наружные, так и внутренние поверхности деталей диаметром от 10 до 500 мм и более.
В чем же здесь секрет?
Для начала просто сравним некоторые данные. Обработка резцом детали из незакаленных сталей обычно дает 4–5 класс шероховатости. После обработки БУФО (за один проход излучателя ультразвука) – 10 класс шероховатости поверхности с Ra ~ 0,1 мкм. Если детали обработаны точением или шлифовкой на 8 класс – БУФО дает возможность получить 11–12 класс шероховатости с Ra ~ 0,05–0,025 мкм с одновременным упрочнением поверхностной структуры. Как это получается?
При воздействии ультразвука – удара излучения о поверхностный слой металла – происходит пластическая деформация микронеровностей поверхности. Уникальность технологии состоит в том, что структура металла существенно изменяется. Как установлено академиком РАЕН В.П. Алехиным, на глубине 15–20 мкм от поверхности обработки металла возникают слои наноструктур с размером зерна 5–10 нм. Остаточные напряжения трансформируются в сжимающие.
Микротвердость обработанного слоя стали, например, увеличивается на 5–35%. Повышается усталостная прочность, увеличивается до 90% опорная поверхность. Некруглость геометрии детали после резца снижается на 25–30%. При условии твердого точения детали в размере использование БУФО тоже исключает необходимость применения шлифовальных станков. Таким образом, становится реальной технология обработки деталей без съема ее с центров, за один «установ».
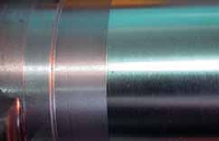
Согласно санитарно-эпидемиологическому заключению, технология БУФО соответствует государственным санитарно-эпидемиологическим правилам и нормативам, безвредна, использовать ее на производстве практически безопасно.
Пятнадцать патентов и признание
Что особенно приятно осознавать – в мировом машиностроении пока нет аналогов технологиям и оборудованию БУФО. На них выдано 15 патентов РФ. Но уж коли дело успешно начато, его не грех продолжать. Благо что интеллектуальный потенциал Центра такое вполне позволяет.
И хоть говорят в народе, что бесконечно улучшать – только портить, питерские исследователи возможностей ультразвука напрочь опровергают эту старую «истину». Обладание авторскими разработками по части промышленного использования мощного УЗ-излучения плюс собственное производство оборудования дают возможность регулярно пополнять ассортимент выпускаемой продукции. А потребитель, он все видит.
В активе Центра – победы в многочисленных тендерах на поставку оборудования для нефтегазового комплекса, электроэнергетики, машиностроения, металлургии и других отраслей промышленности. Приставки БУФО уже активно используют на более чем 350 заводах в России, а также на предприятиях в странах ближнего и дальнего зарубежья – на Украине, в Белоруссии, Латвии, Казахстане, Словакии, Китае и др. Технологию
БУФО высоко оценили специалисты Международного корпуса экспертов (АВLE), она стала постоянной участницей многих международных выставок, где неоднократно получала престижные призы.