При продувке в конвертерной ванне часто возникают ситуации, при которых происходит чрезмерное вспенивание шлаковой фазы, что в дальнейшем приводит к выбросам шлакометаллической эмульсии из агрегата, снижению производительности и выхода годного металла, ухудшению экологической обстановки в цехе и организации работ [1, 2]. Интерес, проявляемый к вспениванию шлаков и эмульгированию металла в шлак, постоянно возрастает, поскольку кинетика этого процесса во многом определяется развитием участвующих в химических реакциях поверхностей раздела. Распространена точка зрения [3, 4], что идеальным вариантом предупреждения чрезмерного вспенивания и выбросов является оптимальная организация дутьевого режима плавки, под которым понимается продувка при переменном положении фурмы и возможный временной график изменения количества вдуваемого в ванну кислорода. В то же время при существующем уровне развития контроля и управления шлаковым режимом конвертерного процесса, непостоянстве состава и температуры чугуна, меняющейся геометрии и температуре футеровки эти мероприятия не всегда эффективны.
Основными причинами выбросов обычно считают повышенное содержание оксидов железа в шлаке и взрывной характер обезуглероживания, одновременное увеличение скорости окисления углерода и склонность шлака к вспениванию, а также плохое перемешивание ванны [5]. Очевидно, связь между скоростью обезуглероживания и изменением уровня ванны существует, однако процесс обезуглероживания расплава не является основной причиной выбросов. Это подтверждают «горячие» плавки или плавки со «свернутым» шлаком, которые характеризуются высокой скоростью обезуглероживания, но проходят без выбросов при пониженном уровне шлакометаллической эмульсии, а часто и при отсутствии таковой [6].
В соответствии с современными представлениями [7, 8] основной причиной чрезмерного вспенивания является продолжающееся в шлаке обезуглероживание корольков металла, при этом выделяющиеся мелкие пузыри монооксида углерода стабилизируют эмульсию и пену. В то же время интенсивность выделения пузырей газа в шлакометаллической эмульсии определяется не только количеством и размером корольков и концентрацией в них углерода, но и физико-химическими свойствами шлака.
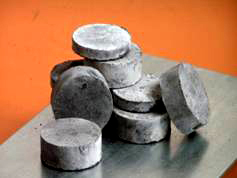
В результате проведенных исследований была разработана технология получения на основе фторуглеродистых отходов алюминиевой промышленности синтетических легкоплавких флюсов оптимального для конвертерной плавки гранулометрического и химического состава [10, 11]. Химический состав кусковых и брикетированных синтетических флюсов представлен в табл. 1. Приведенные данные показывают, что синтетические флюсы являются комплексными органоминеральными соединениями: органическая часть синтетических флюсов представлена углеродом, обеспечивающим необходимый температурный режим для протекания окислительных процессов; минеральная часть — фтористыми солями натрия и алюминия, что позволяет активно участвовать в шлакообразовании и разжижении конвертерных шлаков.
Таблица 1. Химический состав синтетических флюсов | |||||||||
Содержание, % элементов сухой массы | |||||||||
С |
Са |
F |
Na |
AI |
Fe |
Si |
Mg |
S |
К |
Кусковой синтетический флюс, крупность 5-50 мм, Wtr = 1 %, vr/vdaf = 1,7/2,6 % | |||||||||
30-50 |
2-6 |
15-20 |
15-20 |
4-6 |
0,2-0,4 |
0,2-0,5 |
0,4-0,5 |
0,1-0,2 |
0,2-0,3 |
Брикетированный синтетический флюс, крупность 30x40x70 мм, Wtr = 2,4 %, vr/vdaf = 2,1/2,5 % | |||||||||
30-50 |
10-20 |
15-20 |
10-15 |
3-5 |
0,5-1,0 |
0,1-0,2 |
0,1-0,3 |
0,2-0,3 |
0,3-0,5 |
Примечание. Wtr — влажность, vr/vdaf — выход летучих. |
С целью изучения особенностей вспенивания шлака и поиска эффективных способов управления шлаковым режимом конвертерной плавки при использовании синтетических флюсов изучали физико-химические характеристики, фракционный состав продувочных шлаков и «шлаков выбросов» при выплавке низкоуглеродистых марок стали в 350-тонных конвертерах ОАО «Западно-Сибирский металлургический комбинат» (ЗСМК). Продувку расплава кислородом осуществляли четырехсопловой фурмой с интенсивностью 900—1200 м3/мин в соответствии с технологической инструкцией, принятой в цехе.
Во время чрезмерного вспенивания шлака, т. е. при появлении выбросов или переливов через горловину конвертера, специальным устройством отбирали пробы шлакометаллической эмульсии. После извлечения из них неусвоенной извести и металлических корольков и определения массовой доли последних шлаки подвергали химическому анализу, определяли температуру их плавления и вязкость (табл. 2). Выделенные корольки рассеивали по фракциям и подвергали химическому, металлографическому и рентгеноструктурному анализу. Для сравнения анализировали плавки, проведенные по аналогичной технологии, в том числе с промежуточными повадками для отбора проб металла и шлака, на которых чрезмерное вспенивание не наблюдалось.
Установлено, что чрезмерное вспенивание шлака, сопровождающееся выбросами, происходило чаще всего в течение трех интервалов времени продувки: наиболее часто непосредственно после наводки шлака и перевода фурмы в рабочее положение, т. е. в период, соответствующий 25—30 % времени продувки; значительно реже в период интенсивного выгорания углерода (50—60 % времени продувки) и на заключительном этапе плавки (70—90 % времени продувки).
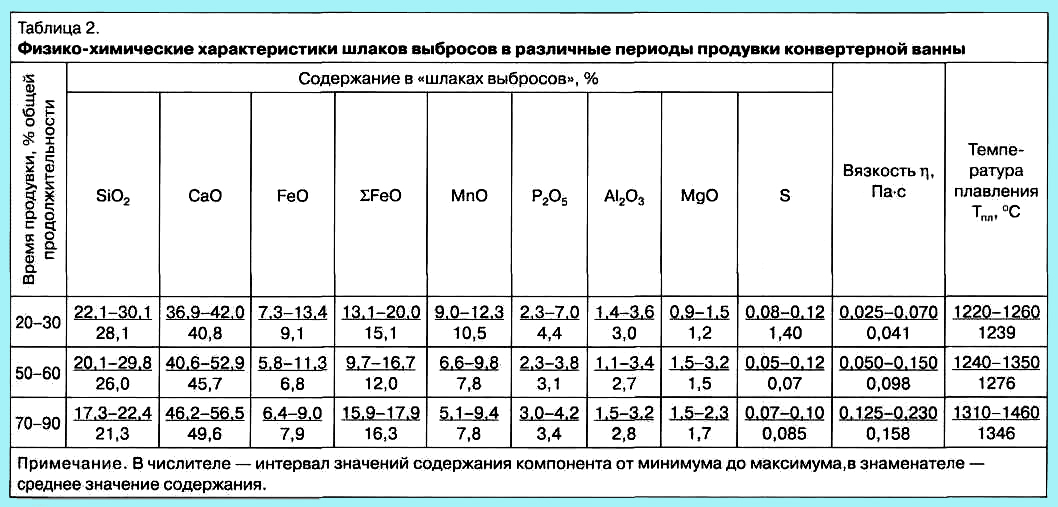
Шлаки, отобранные в первый из указанных интервалов времени, вспенены очень мелкими пузырьками монооксида углерода (до долей миллиметра), разделенными между собой тонкими шлаковыми прослойками. Температура плавления таких шлаков колеблется в пределах 1200—1260°С (рис. 1), а вязкость при температурах, соответствующих моменту выбросов шлакометаллической эмульсии из конвертера, составляет 0,025—0,07 Па•с. Даже при относи-тельно малых значениях вязкости, наряду с плохо укрупняющимися и медленно всплывающими пузырьками монооксида углерода, вспениванию шлака способствует его повышенная окисленность. Причем более высокая окисленность наблюдается в плавках с «холодным» началом операции. Гетерогенность первичных шлаков на плавках с выбросами решающего влияния на вспенивание не оказывала, в то же время относительно низкая основность шлака опытных плавок и наличие в нем неусвоенной извести способствовали процессу образования вспененной шлако-металлической эмульсии.
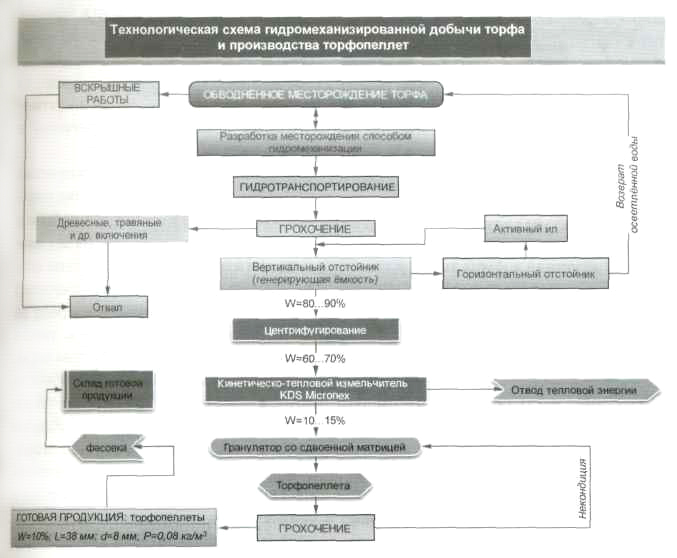
Рис. 1. Изменение температуры плавления шлаков выбросов (точки — температура плавления, линии — области плавления шлаков)
В следующий период, соответствующий 50—60 % времени продувки, процессу вспенивания шлака наряду с отмеченными факторами способствует энергичное развитие реакции обезуглероживания. При этом «шлаки выбросов» вспенениваются относительно более крупными пузырьками монооксида углерода (СО), наличие в них кусочков неусвоенной извести свидетельствует о замедленном шлакообразовании. Температура плавления шлаков составляет 1240—1360°С и более, вязкость достигает 0,15— 0,18 Па-с (рис. 2).

Рис. 2. Зависимость вязкости «шлаков выбросов» от температуры. Заштрихованы области температур плавления шлаков: а - 30-40 %; б— 50-60 %, в — 70-90 % времени продувки
На заключительном этапе плавки (70—90 % времени продувки) температура плавления шлаков достигает 1310—1460°С, их вязкость колеблется в пределах 0,15-0,23 Па-с. Как правило, и в этом интервале времени продувки плавок с выбросами отмечалось наличие в шлаках неусвоенной извести, вспененность его крупными пузырьками СО, большой интервал температур плавления шлаков (свидетельствующий об их неуваренности), высокая окисленность шлаков (на 5-8 % выше, чем в сравнительных плавках) и высокая доля гематита в оксидах железа.
На сравнительных плавках при более высокой основности шлаков вязкость, как правило, была
более низкой. В то же время независимо от вязкости склонность шлака к вспениванию возрастала при увеличении содержала SiO2 и, соответственно, уменьшении основности шлаков.
Представляет интерес характер изменения общего содержания металлических корольков и их фракционного состава в «шлаках выбросов» на опытных плавках. Как видно из рис. 3, изменение относительной массы металлических корольков в шлаках соответствует характеру изменения скорости обезуглероживания металла и свидетельствует о том, что основным источником корольков является вынос их из реакционной зоны потоком отходящих газов. При этом интенсивность образования этих газов определяется скоростью обезуглероживания расплава. Меняется и фракционный состав корольков (см. рис. 3). В начальный период продувки масса мелких фракций корольков (<1 мм), задерживающихся в шлаке, составляет до 50 % их общей массы. Этому способствует высокая окисленность и вязкость шлака. Обезуглероживание таких корольков, очевидно, и приводит к образованию мелких газовых пузырьков в шлаках, при этом осаждение в слое эмульсии относительно крупных корольков (1—3 мм) в этот период продувки происходит сравнительно быстро. В период интенсивного обезуглероживания (50—60 % времени продувки) в результате дробления металла повышается доля наиболее мелких корольков фракции (<0,45 мм) и снижается количество крупных корольков (>2 мм). В заключительный период продувки, несмотря на продолжающийся рост основности и вязкости шлака, общее количество корольков в шлаке уменьшается в результате снижения их выноса из реакционной зоны, при этом значительно повышается доля в шлаке более крупных корольков (1,1—2 и 2,1—3 мм). Это может быть связано с развитием реакции обезуглероживания на поверхности футеровки конвертера и выносом пленок металла в шлак в зоне минимального воздействия газовых струй.
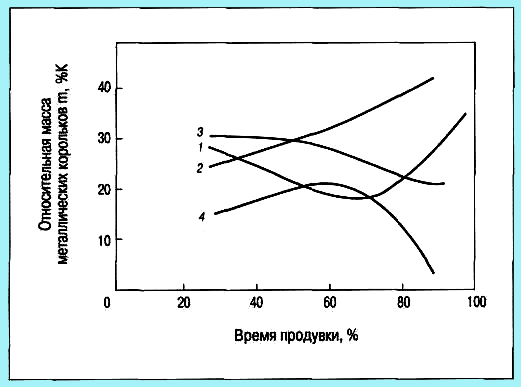
Рис. 3. Изменение массы и фракционного состава корольков в «шлаках выбросов» (1 — 3—2,1 мм; 2 — 2—1,1 мм; 3 — 1,0—0,45 мм; 4 — менее 0,45 мм)
Количество и распространение корольков по фракциям зависят также от гетерогенности шлакового расплава. В связи с этим на «горячих» плавках с нормальным шлаковым режимом возможно несколько отличное от рассмотренного массовое содержание корольков в шлаке.
Наличие корольков в среде с высоким окислительным потенциалом и низким ферростатическим давлением обеспечивает более благоприятные условия рафинирования последних, что подтверждает химический анализ корольков. Максимальный перепад концентрации углерода между металлической ванной и корольками (до 1 %) наблюдался для первой группы «шлаков выбросов», соответствующих начальному периоду продувки. При этом разница концентраций возрастала с уменьшением фракции корольков, что, очевидно, связано с большей удельной поверхностью последних.
Установлено (см. табл. 2), что шлаки плавок с выбросами, как правило, имеют более низкую основность первичных шлаков и более медленный темп нарастания ее по ходу плавки. Если на сравнительных плавках с повалками основность шлаков обычно составляла 2,1—2,5 в начале и до 4,8 в конце операции, то в плавках с выбросами этот показатель был в пределах от 1,3 в начале до 3 единиц в конце плавки. Визуальное сравнение закристаллизовавшихся проб шлака сравнительных плавок и плавок с выбросами показало, что в последних, особенно в периодах начала и середины операции, содержались частицы неусвоенной извести размером до 8—10 мм. В конце плавки (70—90 % времени продувки) в шлаке явных частиц извести не обнаружили. Однако шлаки вы-глядели неуваренными, что также свидетельствует о наличии неусвоенной извести. Шлаки сравнительных плавок с повадками аналогичных периодов были более гомогенными и уваренными. Пониженную основность шлаков при прочих равных условиях можно объяснить только температурными условиями в ванне конвертера, влияющими на степень ассимиляции извести.
Следует отметить, что при использовании синтетических флюсов наблюдалось улучшение показателей тепловой стороны процесса за счет сокращения продолжительности периода наводки шлака и снижения тепловых потерь, имеющих место при бесшлаковой продувке, а также благодаря дополнительному введению в расплав углеродсодержащих составляющих материала. При этом установлено, что динамика горения углерода синтетических флюсов значительно зависит от их фракции. Горение пылевидных частиц синтетических флюсов крупностью 0-0,08 мм начинается раньше горения частиц кокса аналогичной крупности и протекает в области более низких температур. При этом скорости горения углерода синтетических флюсов и кокса на различных стадиях выгорания достаточно близки. При увеличении крупности частиц синтетических флюсов и кокса происходит сдвиг динамических кривых приведенной скорости убыли массы образцов в область более высоких температур, при этом для синтетическою флюса в большей степени (рис. 4). Увеличение крупности кокса не приводит к изменению скорости горения, а увеличение крупности синтетического флюса существенно снижает скорость горения. Это можно объяснить уменьшением поверхности реагирования материала с окислителем, так как вследствие низкой пористости синтетического флюса реакция обезуглероживания развивается только на внешней поверхности материала. В области высоких температур (свыше 900 °С) процесс горения интенсифицируется, и скорость обезуглероживания синтетического флюса резко возрастает, превышая скорость горения кокса, что обусловлено расплавлением минеральной части синтетического флюса и раскрытием пор.
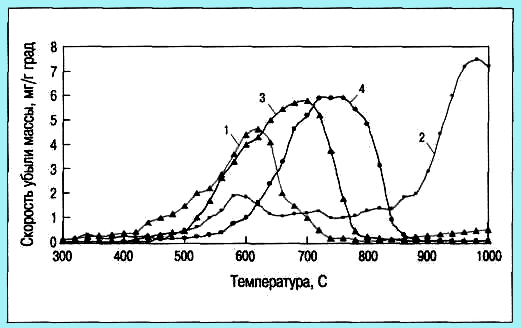
Рис. 4. Зависимость приведенной скорости убыли массы от температуры нагрева синтетического флюса и кокса:
1 — синтетический флюс, фракция 0—0,08 мм;
2 — синтетический флюс, фракция 2—3 мм;
3 — кокс, фракция 0—0,08 мм;
4 — кокс, фракция 2—3 мм
С целью оценки экологических последствий использования синтетических флюсов в конвертерной плавке были проведены исследования поведения содержащегося в составе синтетических флюсов фтора методом термодинамического моделирования с использованием программного комплекса «Терра». При проведении расчетов принято, что синтетические флюсы вводятся в конвертер рассредоточенно по ходу продувки непосредственно в расплавленный шлак, температура которого составляет 1450—1650°С. Химический состав термодинамической системы в этот период рассчитывали на основе данных о химическом составе и количестве синтетических флюсов, шлака и газовой фазы. Полученные данные использовали для расчета материального баланса фтора при его распределении между шлаком и газовой фазой в заданном температурном диапазоне. В результате проведенных расчетов установили, что в условиях конвертерной плавки 46,4—48,8 % фтора переходит в шлак в составе CaF2; 51,2—53,6 % — в газовую фазу, главным образом в составе фторидов натрия NaF (37,4-45,65 %), Na2F2 (3,56-16,57), Na,F, (0,06-0,5), а также фторидов кальция CaF2 (0,24—3,34), калия KF (0,52-0,62) и магния MgF2 (0,05-0,36 %). Абсолютное содержание CaF2 в конвертерном шлаке составляет 0,68—0,7 %, а содержание фтористых соединений в конвертерном газе — 9,2—9,5 %, в том числе 6,8-8 % NaF; 0,62-2,46 Na2F2; 0,01-0,09 Na3F3, 0,04-0,54 CaF2, 0,13-0,14 KF, 0,01-0,07 % MgF2. Динамика распределения фтора между соединениями шлаковой и газовой сред представлена на рис. 5. Приведенные данные показывают, что при увеличении температуры шлака с 1450 до 1650°С количество переходящего в газовую фазу фтора возрастает с 52,3 до 53,6 %, а в шлак — снижается с 47,7 до 46,4 %. При этом происходит перераспределение фтора между компонентами газовой фазы: возрастает доля фтора в составе NaF, CaF2, MgF2 и KF при снижении доли фтора в составе Na2F2 и Na3F3.
Рис. 5. Распределение фтора между шлаком и газовой фазой в конвертере
Следует отметить, что содержание CaF2 в конвертерном шлаке при применении синтетических флюсов ниже, чем при использовании плавикового шпата (более 1 %). При этом высокотемпературный остеклованный конвертерный шлак препятствует миграции фтора в окружающую среду. Фториды газовой фазы в процессе мокрой газоочистки за конвертером подвергаются гидролизу с образованием сильноразбавленного водного раствора HF (фтороводородная кислота). В условиях конвертерных цехов оборотная вода системы газоочистки характеризуется очень высокой щелочностью (до 11 — 12 рН), что связано с высоким содержанием извести в составе конвертерной пыли. Это приводит к образованию прочных карбонатных отложений и зарастанию трубопроводов. Подкисление воды в системе газоочистки будет способствовать снижению ее щелочности. С другой стороны, высокое содержание извести в оборотной системе конвертерной газоочистки обеспечит высокую эффективность осаждения фтора в составе образующегося фторида кальция CaF2, относящегося к малоопасным веществам.
Исследования подтвердили, что шлаки более поздних периодов плавки вспениваются из-за их высокой гетерогенности и вязкости. Более высокая механическая прочность синтетического флюса по сравнению с плавиковым шпатом обеспечивает снижение доли материала мелких фракций, подверженных интенсивному выносу из агрегата высокоскоростными потоками отходящих газов. При этом процесс шлакообразования протекает достаточно энергично, и если по ходу продувки потребуются дополнительные мероприятия для сохранения жидкоподвижности шлака, то регламентированная присадка синтетического флюса позволяет предупредить повышенное вспенивание шлака. Условия конвертерной плавки и системы очистки конвертерных газов обеспечивают безопасность использования синтетических легкоплавких флюсов для окружающей среды.
Библиографический список
1. Баптизманский В. И. Теория кислородно-конвертерного процесса. — М.: Металлургия, 1975. — 375 с.
2. Баптизманский В. И., Меджибожский М. Я., Охотский В. Б. Конвертерные процессы производства стали. — Киев-Донецк: Вища школа, 1984. -344 с.
3. Колпаков С. В., Тедер Л. К., Дубровский С. А. и др. Управление конвертерной плавкой. — М.: Металлургия, 1981.— 144 с.
4. Коотц Т., Беренс К., Маас Г. и др. Некоторые вопросы теории кислородно-конвертерного процесса. Дискуссия // Черные металлы. 1965. № 15. С. 42—52.
5. Баптизманский В. И., Яновский И. Л., Жигулин В. Н. и др. Исследование причин выбросов и дутьевого режима в кислородном конвертере // Сталь. 1967. №4. С. 309-312.
6. Яновский И. Л., Жигулин В. И., Рубинский П. С. и др. Изучение причин выбросов из конвертеров // Изв. вузов. Черная металлургия. 1965. № 5. С. 34-39.
7. Баптизманский В. И., Охотский В. Б. Физико-химические основы кислородно-конвертерного процесса. — Киев-Донецк: Вища школа, 1981. — 183 с.
8. Чернятевич А. Г., Зарвин Е. Я., Волович М. И. Наблюдение через прозрачную стенку за поведением конвертерной ванны при продувке // Изв. вузов. Черная металлургия. 1975. № 2. С. 37—42.
9. Айзатулов Р. С, Буймов В. А., Машинский В. М. и др. Использование шлакообразующих материалов при выплавке стали в конвертерах // Сталь. 1995. № 1.С. 20-21.
10. Волынкина Е. П., Макарчук В. В., Халаман Н. А. Способ получения комплексных синтетических флюсов для черной металлургии // Патент РФ № 2354707. С21ВЗ/02. Заявл. 30.05.2007. Опубл. 10.05.2009.
11. Синтетические легкоплавкие флюсы на основе фторуглеродистых отходов алюминиевой промышленности / Е. П. Волынкина, Е. В. Протопопов,
B. В. Макарчук, Н. А. Халаман // Экология производства. Металлургия и машиностроение. 2008. № 1(10).
C. 4-6.
Статья из журнала "Черные металлы", сентябрь, 2011 г.