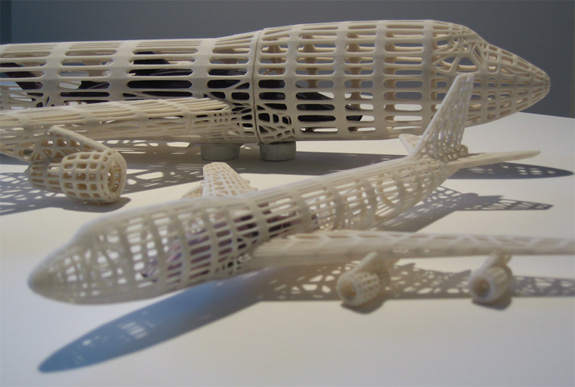
Авторы: Смирнов Владимир Григорьевич, Полудин Алекcандр Витальевич, Галкин Андрей Валерьевич, Зобнин Виктор Иванович, Мальцевич Вячеcлав Владимирович
Изобретение относится к области самолетостроения, в частности к способу изготовления каркасных силовых элементов конструкции летательного аппарата преимущественно из титановых сплавов. В способе изготовления профилей с регламентированной кривизной продольное сечение профиля формируют при температуре выше температуры полиморфного превращения в канале стапеля, имеющего регламентированные геометрические размеры, производя последовательное заполнение канала по мере выпрессовки профиля из матрицы. Правку и термообработку профиля осуществляют непосредственно в стапеле без его разборки. К матричному узлу устройства крепится съемный разборный стапель, в котором выполнен канал, форма внутреннего поперечного сечения канала частично или полностью подобна наружной форме поперечного сечения прессуемого профиля. Внутренние размеры сечения канала выполнены на 0,5-3 мм больше подобных наружных размеров сечения профиля. Канал выполнен таким образом, что пространственное положение осей его сечений в продольном направлении совпадает с пространственным положением осей сечений готового профиля. Изобретение обеспечивает повышение качества получаемых профилей и производительности за счет совмещения технологических операций прессования и формирования его конфигурации в осевом направлении в стапеле. 3 ил.
Основой конструкции фюзеляжа и крыльев самолета является тонкостенная пространственная оболочка, подкрепленная изнутри силовым каркасом. Простые каркасные детали обычно изготавливаются из прессованных или гнутых профилей различного сечения и, как правило, имеют в продольном направлении изогнутые в пространстве оси.
В основе своей существующие технологии базируются на осуществлении операций, которые по времени выполнения не имеют жесткой связи, и для каждой технологической операции используется полностью своя технологическая оснастка, при этом перед каждой операцией производится предварительный нагрев заготовки. Технологические операции осуществляются в следующей последовательности:
- - прессование профиля (формирование геометрической формы поперечного сечения);
- - правка растяжением с обеспечением технических требований по прямолинейности, кривизне и скручиванию, обрезка захватов;
- - термообработка (снятие внутренних напряжений и получение заданных свойств материала);
- - гибка и правка профиля (формирование геометрической формы профиля в осевом направлении);
- - термообработка (снятие внутренних напряжений и получение заданных свойств материала).
Из-за неоднородности физико-механических свойств материала по длине и в поперечных сечениях заготовки геометрическая форма профилей в процессе деформации и термообработки подвергается значительным искажениям и в общем случае требуются значительные трудовые, временные и финансовые ресурсы для достижения тех результатов, которые предусмотрены техническими условиями на готовую продукцию.
Поскольку требование к геометрической форме профиля в самолетостроении жесткие, то необходимо максимально нивелировать вредные факторы, искажающие геометрию профиля.
Известен способ термосиловой обработки (термоправки) осесимметричных длинномерных деталей, включающий предварительную обработку детали, закрепление на детали распорных втулок, установку детали с втулками в многослойный стапель, фиксацию детали за счет контакта со сферической поверхностью, установку стапеля с деталью в печь, нагрев до определенной температуры, выдержку до достижения необходимого уровня равномерности деформаций и охлаждение (патент РФ

Недостатком изобретения является его узкая специализация, которая позволяет его применение только для обработки изделий типа валов, которые прошли предварительную обработку.
Известны способ и устройство для изготовления криволинейных полых профилей, позволяющие получить прессованные профили с кривизной, которая может быть рассчитана заранее и легко воспроизводится, при этом даже у сложных профилей площадь сечения после гибки не изменяется по сравнению с площадью сечения до гибки (европейский патент

Способ включает изгиб профиля поперечной силой одновременно с прессованием или непосредственно после него, при котором в процессе прессования составляющая изгибающего усилия воздействует на сечение образующих стенок профиля как растягивающая или сжимающая сила, при этом гибочный инструмент расположен в свободном пространстве после выхода профиля из матрицы. Профиль подвергается операции гибки нажимным устройством при температуре прессования сразу после выхода из матрицы. В принципе изобретение позволяет задать любые углы путем соответствующей настройки гибочного приспособления, в том числе и при пространственной гибки, а также закрутку профиля.
Основным недостатком изобретения является его относительно небольшая точность, обусловленная низкой точностью операции гибки, на которую будут наслаиваться погрешности операций термообработки. Потенциально искажение геометрических размеров и формы может возникать как в сечении, так и по оси профиля, что ведет к нестабильности технологического процесса (делает проблематичным использование данной технологии в самолетостроении).
Целью данного изобретения является предложение способа для изготовления криволинейных профилей, позволяющего получить прессованный профиль, удовлетворяющий требованиям точности, предъявляемым к изделиям, используемым в современных самолетных конструкциях, и устройства для его осуществления.
Техническим результатом, достигаемым при применении предлагаемого изобретения, является совмещение технологических операций прессования профиля и формирования его конфигурации в осевом направлении в стапели, а также использование данного стапеля в процессе термической обработки, что позволяет:
- - изготовлять прессованный профиль, по точности близкий или равноценный механически обработанному профилю, т.к. наружный профиль контура соответствует внутреннему механически обработанному контуру стапеля;
- - в процессе термообработки происходит термоправка изделия в стапеле вследствие этого исключается накопление погрешностей в геометрических размерах и форме профилей, возникающих в процессе термообработки изделий из-за неоднородности физико-механических свойств материала по длине, а также в поперечных сечениях заготовки, в результате происходит повышение эксплуатационной точности готовых изделий.
Указанный технический результат достигается тем, что в способе изготовления профилей с регламентированной кривизной, включающем формирование поперечного сечения профиля прессованием, формирование продольного сечения профиля непосредственно после прессования, отделение пресс-остатка, правку и термообработку, продольное сечение профиля формируют при температуре выше температуры полиморфного превращения в канале стапеля, имеющего регламентированные геометрические размеры, производя последовательное заполнение канала по мере выпрессовки профиля из матрицы, а правку и термообработку профиля осуществляют непосредственно в стапеле без его разборки.
Для уменьшения сил трения между каналом стапеля и внутренней поверхностью профиля на поверхность канала стапеля наносится смазка.
Предложенный способ реализуется с помощью устройства для изготовления профилей с регламентированной кривизной, содержащего пресс с матричным узлом, к матричному узлу крепится съемный разборный стапель, в котором выполнен канал, форма внутреннего поперечного сечения канала частично или полностью подобна наружной форме поперечного сечения прессуемого профиля, а внутренние размеры сечения канала выполнены на 0,5-3 мм больше подобных наружных размеров сечения профиля, при этом канал выполнен таким образом, что пространственное положение осей его сечений в продольном направлении совпадает с пространственным положением осей сечений готового профиля.
Изобретение поясняется чертежами, где на фиг.1 показано устройство для изготовления профилей с регламентированной кривизной, на фиг.2 - поперечное сечение профиля, продольный вид профиля, на фиг.3 - продольный вид профиля.
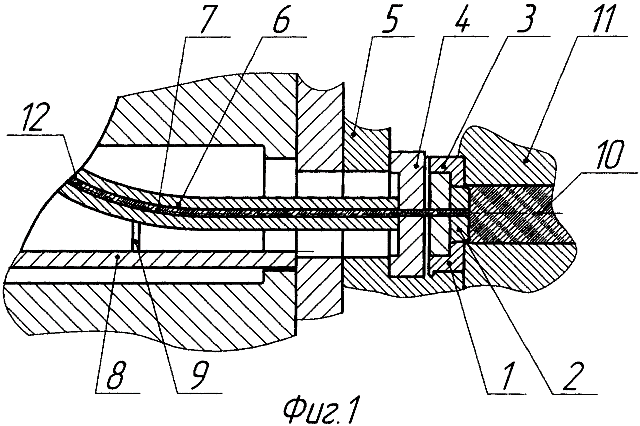
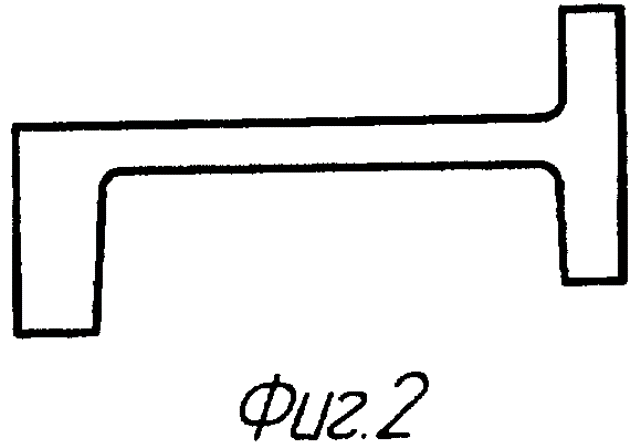
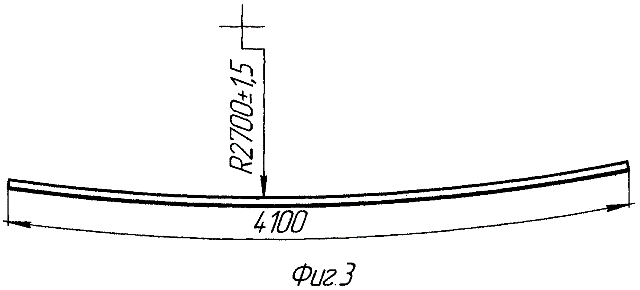
Приспособление содержит (фиг.1) матричный узел 1, состоящий из матрицы 2, матрицедержателя 3, опорного кольца 4, матричный узел крепится к инструментальной доске 5, к опорному кольцу крепится разъемный стапель 6, в котором расположен канал 7, стапель монтируется на стол пресса 8 посредством кронштейнов 9.
Способ осуществляется следующим образом: заготовку 10 размещают в контейнере 11, под действием пресс-штемпеля (не показан) происходит распрессовка заготовки 10 через матричный узел 1. Прессованный профиль 12 из матричного узла поступает в канал 7 стапеля. Скорость прессования титановых сплавов достаточно высокая, а размерная длина профиля подбирается из условий, чтобы температура профиля не опускалась ниже температуры полиморфного превращения в процессе размещения его в канале стапеля. Это позволяет получить профиль, имеющий кривизну в различных пространственных плоскостях, а также его закрутку. Для уменьшения сил трения на поверхность канала рекомендуется наносить смазку. Для предотвращения заклинивания профиля в канале стапеля геометрические размеры его сечений выполнены на 0,2-3,0 мм больше геометрических размеров сечения профиля. После окончания операции прессования и отделения пресс-остатка стапель вместе с находящимся в нем профилем снимают со стола пресса. Последующая термообработка профиля производится в стапеле, для чего стапель размещают в нагревательных устройствах. После термообработки в материале профиля снимаются внутренние напряжения, и его геометрические размеры не искажаются после извлечения из стапеля.
Пример конкретного выполнения.
На горизонтальном гидравлическом трубопрофильном прессе усилием 3150 тс выпрессовывают профиль (фиг.2 и 3), имеющий в поперечном сечении площадь S=39,231 см2, длиной 4100 мм и радиусом кривизны R=2700 мм из сплава Ti-6Al-4V.
Нагрев заготовок производится до температуры 1030-1060°С, в процессе деформации наблюдается деформационный разогрев металла до температуры 1090-1120°С. После размещения заготовки выполняют прессование профиля со скоростью прессования порядка 1 м/с. Вся операция прессования длится около 4 секунд. За это время материал профиля не охлаждается ниже температуры полиморфного превращения 990°С, практически размещение профиля в канале стапеля происходит в

Профиль со стапелем размещают в электрической печи, производят термообработку по режиму: 760°С, выдержка 2 часа, охлаждение на воздухе.
Преимущество данного способа заключается в том, что он:
- - позволяет изготовить профили с регламентированной кривизной, которые максимально приближены по форме к готовым изделиям и соответствуют требованиям, предъявляемым к современным самолетным конструкциям;
- - расширяет возможности стандартного прессового оборудования;
- - повышает производительность процесса изготовления профилей за счет устранения трудоемких операций правки и повышает качество получаемых профилей.