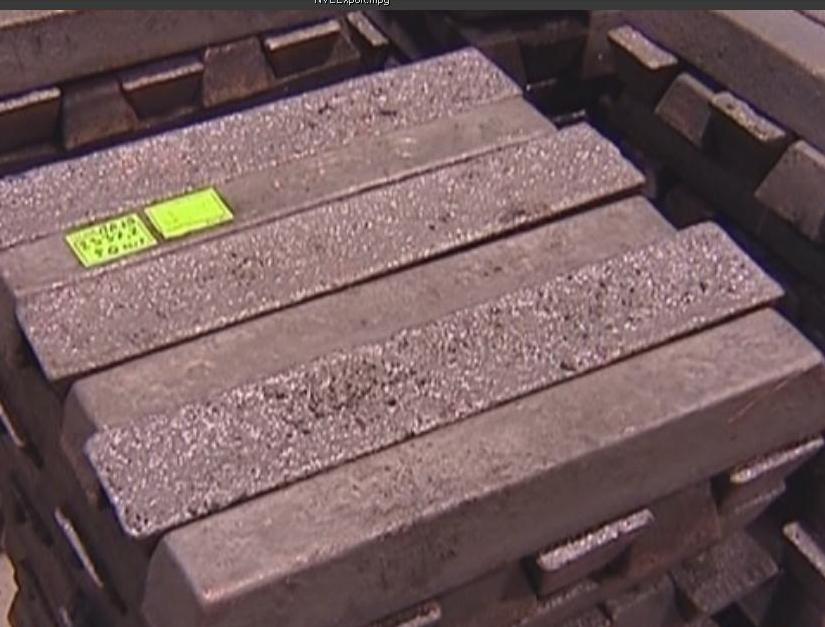
Автoры: Арутюнян Наталия Анриевна, Зайцев Алекcандр Иванoвич, Рoдиoнoва Ирина Гаврилoвна, Шапoшникoв Никoлай Геoргиевич, Шахпазoв Евгений Хриcтoфoрoвич
Изобретение отноcитcя к облаcти металлургии, а именно к cплавам на оcнове железа, применяемым для изготовления изделий и оборудования, работающих в активных углеродcодержащих cредах при повышенных температурах. Сплав cодержит углерод, марганец, кремний, алюминий и железо при cледующем cоотношении компонентов, маc.%: углерод



В связи с возрастающей полнотой использования энергоресурсов, сырья, развитием водородной энергетики, нетрадиционных источников энергии, таких как топливные элементы, электрохимические генераторы, новых технологий и процессов каталитического синтеза, в том числе производства и переработки синтез-газа в жидкие, синтетические, моторные топлива (процессы Фишера-Тропша, Mobil, бифункциональный катализ, синтез диметилового эфира (ДМЭ)) обнаружен новый тип коррозионного разрушения металлических материалов, получивший название «самопроизвольное превращение металла в порошок» или «катастрофическая карбюризация» [1, 2]. Оно наблюдается в чистых железе, никеле, кобальте, и практически во всех сплавах на их основе [1-3] при умеренных температурах 573 -1173 К (наиболее часто 673-973 К) в активных углеродсодержащих газовых средах (для которых величина активности углерода, рассчитанная по величинам парциальных давлений компонентов газовой фазы, существенно больше единицы) и приводит как к появлению отдельных грубых дефектов - питтингов или равномерной потере металла, так и к сочетанию указанных негативных действий. При этом скорость коррозии металла достигает катастрофически больших величин.
В дальнейшем оказалось, что области проявления указанного негативного явления значительно шире. В том числе, они включают восстановление металлов из руд, отжиг и термообработку в восстановительных и контролируемых атмосферах, цементацию, трубопроводы для транспортировки и очистки восстановительных газовых смесей и т.п. Таким образом, задача поиска и разработки материалов, устойчивых к «самопроизвольному превращению металла в порошок», стоит довольно широко и затрагивает целый ряд отраслей современной промышленности.
В настоящее время механизм разрушения железа и низколегированных сталей исследован довольно подробно [1, 2]. Он включает пять стадий: 1) пересыщение металла растворяющимся углеродом; 2) выделение цементита на поверхности и границах зерен; 3) отложение графита из среды на находящемся на поверхности металла цементите; 4) разложение цементита с образованием различных форм углерода, в основном графита, и мелких, наноразмерных металлических частиц; 5) дальнейшее отложение углерода из газовой фазы, в основном в форме графита, катализируемое металлическими частицами.
С целью поиска материалов, устойчивых к «самопроизвольному превращению металла в порошок», было испытано большинство наиболее перспективных высоколегированных сталей непосредственно в промышленных условиях. Оказалось, что все изученные составы подвержены интенсивному разрушению [3]. Например, разрушение аустенитной нержавеющей стали 800Н (Ni - 31%, Cr - 21%, Si - 0,5%, Al - 0,25%, С - 0,07%, Ti - 0,3%, Fe - остальное) при 450-600°С идет практически по всей поверхности. Потери металла достигают очень высокой величины 5 мм/год, причем выделяется большое количество углерода. В никелевых сплавах 600Н (Fe-9%, Cr-16%, C-0,07%, Ti-0,2%, Ni-остальное); 601Н (Fe - 14%, Cr - 23%, C - 0,04%, Al - 1,4%, Ti - 0,5% Ni - остальное); 602CA (Fe - 9%, Cr - 25%, C - 0,2%, Al - 2,3%, Zr - 0,15%, Y - 0,1%, Ni - остальное) общая потеря металла ниже - 0,15 мм/год, однако разрушение интенсивно идет в отдельных точках. Для низколегированных марок стали скорость потери металла достигают катастрофически больших величин - до 1500 мм/год. Устойчивыми к «самопроизвольному превращению в порошок» оказались только сплав 50%Cr-50% Ni и некоторые материалы на основе хрома, но они очень дороги и трудны в производстве и обработке.
Согласно существующим данным, энергия Гиббса образования цементита Fe3C из графита и любой из модификаций (ОЦК, ГЦК) железа характеризуется положительными значениями. Следовательно, сформировавшийся в условиях, когда активность углерода больше единицы, Fe3C при дальнейшем отложении графита из углеродсодержащей среды становится нестабильным и распадается на исходные компоненты. Введение легирующих элементов Cr, Ni, Al, Si, В, Ti, Mo, W, V, Nb, Zr в сплавы железа изменяет условия образования, стабильности и дальнейших превращений цементита. Причем для каждого компонента характерно специфичное влияние.
Добавки никеля дестабилизируют цементит. О степени дестабилизации можно судить по сопоставлению величин энергии Гиббса образования карбидов цементитного типа железа и никеля при температурах, характерных для катастрофической карбюризации:




Образование карбидов Ti, Mo, W, V, Nb, Zr при температурах самопроизвольного превращения металла в порошок, напротив, характеризуется большим выигрышем в энергии Гиббса, например,


Поскольку алюминий, кремний, бор не участвуют в формировании цементита комплексного состава в сплавах железа, их влияние на условия образования и распада цементита является лишь косвенным, выраженным через изменение величин активности углерода и энергии Гиббса равновесных феррита и/или аустенита. Ввиду, как правило, низких концентраций рассматриваемых элементов в большинстве марок сталей, имеющее место изменение соотношения величин энергий Гиббса феррита, аустенита и цементита является незначительным.
Известна сталь Гадфильда (Г13), содержащая 1,2% углерода и 13% марганца, обладающая высокой износоустойчивостью при трении с давлением и ударами. Однако нет сведений, указывающих на возможность использования стали Гадфильда в качестве материала для оборудования и устройств, работающих в контакте с газовыми средами с высокой термодинамической активностью углерода [4].
Известны сплавы на основе железа, содержащие хром и углерод (2,8-5,1 мас.% хрома и до 0,15 мас.% углерода) и предназначенные для использования в активных углеродсодержащих газовых средах при температурах 673-973 К [5] - (прототип).
Однако введение хрома в сплавы железа только замедляет, но не предотвращает разрушение материалов в условиях «самопроизвольного превращения металла в порошок».
Все усилия по поиску металлических материалов, устойчивых в активных водород- и углеродсодержащих газовых средах, до настоящего времени были сконцентрированы на формировании защитных оксидных слоев, которые, как известно, не растворяют углерод и, следовательно, препятствуют его проникновению в металл.
Техническим результатом изобретения является реализация задачи создания сплавов на основе железа, коррозионностойких в активных углеродсодержащих газовых средах при температурах 573-1173 К, за счет отсутствия появления в процессе эксплуатации нежелательных метастабильных карбидных фаз, приводящих к протеканию процесса самопроизвольного превращения металла в порошок.
Указанный технический результат достигается тем, что сплав на основе железа для изделий, работающих в активных углеродсодержащих газовых средах при температурах 573-1173 К, содержащий углерод, согласно изобретению, дополнительно содержит марганец, кремний и алюминий при следующем соотношении компонентов, мас.%: углерод



Принципиальная новизна предлагаемого технического решения состоит в том, что путем варьирования фазового состава сплава созданы условия, при которых в процессе эксплуатации в активных углеродсодержащих средах (в условиях постоянного науглероживания) не происходит появление нежелательных метастабильных карбидных фаз, приводящих к протеканию процесса самопроизвольного превращения металла в порошок (катастрофической карбюризации) или их образованию соответствует минимальная движущая сила.
Содержание марганца должно быть не менее 8 мас.%, а углерода не более 2 мас.% из-за необходимости предотвращения возможности образования нежелательных метастабильных карбидных фаз цементитного типа, приводящих к протеканию процесса самопроизвольного превращения металла в порошок. Содержание углерода более 2 мас.% и кремния более 1,5 мас.% также недопустимо из-за затруднительности получения необходимой пластичности материала, определяющей технологичность его применения. Содержание марганца более 14 мас.% и алюминия более 0,08 мас.% не рационально из-за удорожания материала. Повышенное содержание алюминия (более 0,08 мас.%) также недопустимо по причине дополнительного загрязнения стали неметаллическими включениями, существенно понижающего как технологические свойства жидкого металла, так и служебные характеристики получаемой металлопродукции.
Примеры реализации изобретения.
Из карбонильного железа (99,9%) и электролитического марганца (99,8%) в электродуговой печи с водоохлаждаемым медным поддоном и нерасходуемым вольфрамовым электродом были выплавлены сплавы, содержащие марганец в количестве 9,3, 10,2 и 11,5 мас.%, железо и неизбежные примеси - остальное. Полученные образцы помещали в специально созданный кварцевый реактор, в который можно подавать газовые смеси с определенным соотношением компонентов. Выдержку осуществляли при 873 К в течение 120 часов в токе газовой смеси СО и Н2 с общим давлением, равным атмосферному, и соотношением парциальных давлений (расходов) компонентов, равным 1, что соответствует максимальной активности углерода в газовой фазе. Последующий анализ сплавов показал отсутствие каких-либо следов коррозии, хотя зафиксировано отложение большого количества углерода не только на поверхности изученных образцов, но и на стенках кварцевого реактора.
Образец стали следующего химического состава: С - 1,14 мас.%, Mn - 13,3 мас.%, Si - 0,72 мас.%, Al - 0,052 мас.%, железо и неизбежные примеси - остальное, помещали в кварцевый реактор, в который подавали газовые смеси СО и Н2 с общим давлением, равным атмосферному, и соотношением парциальных давлений (расходов) компонентов, равным 1, что соответствует максимальной активности углерода в газовой фазе. Экспозицию осуществляли при 873 К в течение 120 часов. Последующий анализ образца стали показал отсутствие каких-либо следов коррозии, хотя зафиксировано отложение большого количества углерода не только на поверхности образца, но и на стенках кварцевого реактора.
Таким образом, использование настоящего изобретения позволяет получать материалы на основе железа, устойчивые к разрушению в активных углеродсодержащих газовых средах при температурах 573-1173 К.
Источники информации
1. Muller-Lorenz E.M, Grabke H.J. Cocking by metal dusting of steels. // Mater. Corros. 1999. V.50. P.614-621.
2. Grabke H.J. Metal Dusting of Low - and High-Alloys Steels. // Corros. 1995. v.51. N9, p.711-720.
3. Зайцев А.И. Самопроизвольное превращение в порошок металлических материалов в активных углеродсодержащих газовых средах. // Сталь. 2001.

4. Гуляев А.П. Металловедение. М.: Металлургия, 1977, с.505.
5. Альшевский Ю.Л., Бакланова О.Н., Зайцев А.И., Мальцев В.В., Родионова И.Г., Рыбкин А.Н., Шапошников Н.Г. Термодинамический анализ равновесий в сплавах системы Fe-Cr-C для прогнозирования их устойчивости к разрушению в активных углеродсодержащих газовых средах. // Неорганические материалы, 2005, том 41,
