Следует отметить, что все четыре стана имеют грибовидные валки и общие размеры используемых заготовок и получаемых гильз.
Для сравнения были выбраны режимы прошивки для получения наиболее «массовых» размеров труб, получаемых на рассматриваемых станах. Параметры заводских режимов и характеристики конечного формоизменения указаны в табл. 2 [1—3].
На рис. 1 показан очаг деформации с рассматриваемыми сечениями и шагами подачи.
Среди особенностей заводских режимов настройки следует отметить получение различных суммарных вытяжек (1,586; 1,64; 2,696; 2,059), что приводит к разной длине шага подачи в сечении входа А и разному числу шагов подачи до граничных точек В, С, D и F (см. рис. 1 и табл. 2).
Так, на стане Челябинского трубопрокатного завода шаг подачи на входе и выходе равен 23,1 и 36,7 мм, углы конусности валка (см. табл. 1) дают длину участка А—В до носка оправки 190 мм, но из-за малого угла подачи (4,15 град.) число шагов подачи перед носком оправки большое, что приводит к максимальной степени деформации сдвига до носка оправки Λв (табл. 3) из всех четырех станов. На стане Северского трубного завода шаг подачи в сечениях А и F равен 38,7 и 61,5 мм (максимальный из всех станов), углы конусности валка дают длину участка А—В 145 мм и самое минимальное число шагов из всех четырех рассматриваемых станов и значение накопленной деформации сдвига, что, возможно, благоприятно скажется на проработке структуры и качестве гильз. На стане Таганрогского металлургического завода шаг подачи составляет 35,3 и 72,7 мм, длина участка А—В равна 216 мм, но из-за большого угла подачи (10 град.) число шагов стоит на втором месте после Северского трубного завода.
Параметры настройки заводских режимов, приведенные в табл. 2 и 3, существенно отличаются. Для более адекватного сравнения четырех прошивных станов был выбран «модельный» режим прошивки заготовки диаметром 325 мм в гильзу 350x50 мм, который можно осуществить на всех рассматриваемых станах. По рекомендации работ [1—3] для этого случая были подобраны обжатия в пережиме un и перед носком оправки u0, приведенные в табл. 4. Так как длина оправки подбиралась под заданное обжатие
Завод (фирма-изготовитель оборудования) /Параметры
|
Челябинский трубопрокатный (ЭЗТМ)* |
Северский трубный (ЭЗТМ) |
Павлодарский трубопрокатный (Danieli) |
Таганрогский металлургический (SMS-Meer) |
Диаметр валка в пережиме DBn, мм |
1150 |
1350 |
1150 |
1150 |
Длины участков валка, мм: | ||||
полная LB |
1400 |
1300 |
950 |
990 |
входного конуса |
490 |
660 |
320 |
285 |
выходного конуса |
720 |
570 |
480 |
575 |
пережима |
190 |
70 |
150 |
130 |
Углы конусности валка, град.: | ||||
на входе φ1 |
4-8 |
3,5 |
2,5 |
2,5 |
на выходе φ2 |
4 |
4,9 |
3,25 |
2,8 |
Углы, град.: | ||||
подачи α |
5-10 |
8-10 |
8-10 |
8-15 |
раскатки β |
6 |
12 |
15 |
15 |
Скорость вращения валков, об/мин |
120 |
50 |
125-155 |
83-113 |
Диаметр, мм: | ||||
заготовки D3 |
430-650 |
300-400 |
210-400 |
210-300 |
гильзы Dr |
300-650 |
300-450 |
220-400 |
220-370 |
Толщина стенки гильзы, мм |
80-120 |
50-110 |
20-50 |
20-50 |
* Проект. |
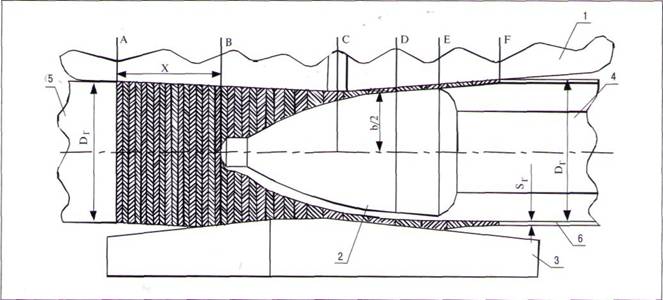
Рис. 1. Схема продольного сечения очага деформации с шагами подачи:
1 — валок; 2 — оправка; 3 — направляющая линейка; 4 — стержень оправки; 5 — заготовка; 6 — гильза; сечения: А — контакт заготовки с валком; В — встреча с оправкой; С — пережим валков; D — начало калибрующего участка оправки; Е — сход гильзы с оправки; F — отрыв гильзы от валков перед носком оправки (u0), то длина оправки на четырех рассматриваемых станах была разная.При сравнении станов разных заводов на одном режиме и угле подачи суммарная вытяжка составляла 1,5, длина шага подачи на входе и выходе (в точках А и F) равнялась соответственно 50 и 75 мм.
В результате различной калибровки валков (см. табл. 1) и длины оправки число шагов и накопленная степень деформации сдвига в граничных точках различались.
Таблица 2. Заводские режимы настройки для получения «массовых» размеров труб
Завод /Параметр |
Диаметр заготовки D3, мм |
Размер гильзы DrxSr мм |
Расстояние между валками to, мм |
Диаметр оправки, d0, мм |
Обжатия, % |
Отношение X/D3 (см. рис. 1) |
Угол подачи α, град. |
Координаты точек (см. рис. 1) |
| ||||||||||||||||
в пережиме uо |
перед носком оправки |
А |
В |
F |
| ||||||||||||||||||||
Челябинский трубопрокатный |
430 |
450x80 |
385 |
275 |
7,5 |
10,5 |
0,44 |
4,15 |
-409 |
-219 |
545 |
| |||||||||||||
Северский трубный |
360 |
360x67,5 |
325 |
214 |
5,4 |
10 |
0,4 |
8 |
-303 |
-158 |
213 |
| |||||||||||||
Павлодарский трубопрокатный |
300 |
328x29 |
270 |
260 |
6 |
10 |
0,61 |
8 |
-363 |
-179 |
522 |
| |||||||||||||
Таганрогский металлургический |
300 |
328x38 |
270 |
235 |
8,5 |
10 |
0,72 |
10 |
-363 |
-147 |
561 |
|
Таблица 3. Параметры циклического формоизменения для заводских режимов, полученные с помощью математической модели [4] для режимов, указанных в табл. 2
Завод |
Параметр | |||||
Число шагов до граничных точек |
Накопленная степень деформации сдвига в граничных точках | |||||
NB |
Nc |
NF |
Λв |
Λс |
ΛF | |
Челябинский трубопрокатный |
8,98 |
16,63 |
32,41 |
5,12 |
9,53 |
13,64 |
Северский трубный |
4,6 |
7,59 |
11,05 |
2,07 |
6,56 |
9,17 |
Павлодарский трубопрокатный |
9,48 |
16,17 |
27,91 |
4,79 |
8,69 |
14,62 |
Таганрогский металлургический |
6,89 |
10,16 |
19,11 |
3,03 |
6,42 |
11,21 |
Завод /Параметр |
Расстояние между валками to, мм |
Обжатия, % |
Отношение X/D3 |
Координаты точек, мм | ||||
U0 |
Uп |
А |
В |
D |
F | |||
Челябинский трубопрокатный |
292 |
5,5* |
10 |
0,34 |
-304 |
-192 |
287 |
453 |
5 |
0,32 |
-285 |
-189 |
416 |
572 | |||
Северский трубный |
286 |
5,9 |
12 |
0,42 |
-321 |
-185 |
213 |
349 |
5 |
0,35 |
-300 |
-194 |
316 |
449 | |||
Павлодарский трубопрокатный |
292 |
6,3 |
10 |
0,58 |
-392 |
-204 |
331 |
515 |
5 |
0,47 |
-365 |
-222 |
482 |
650 | |||
Таганрогский металлургический |
286 |
5 |
12 |
0,44 |
-434 |
-291 |
369 |
596 |
5 |
0,47 |
-355 |
-213 |
488 |
698 | |||
* Числитель — диаметр заготовки D3 = 325 мм, знаменатель —D3 =300 мм. |
По сравнению с другими станами на прошивном стане Северского трубного завода была получена минимальная проработка литой структуры до носка оправки (см. рис. 2, кривые 1—4) и достигается ее максимальное значение на выходе.
Как метод снижения склонности к дефектообразованию, в литературе [5] рекомендуют, по возможности, использовать меньший диаметр заготовки.
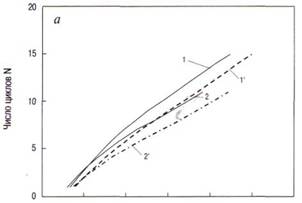
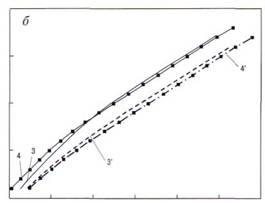
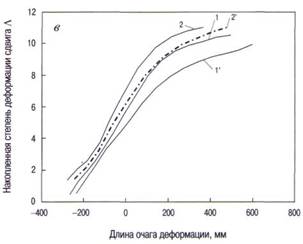
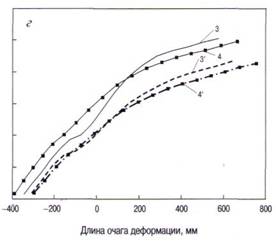
Рис. 2. Распределение числа шагов (а, б) и накопленной степени деформации сдвига (в, г) по длине очага деформации:
1, 1' — прошивной стан Челябинского трубопрокатного завода; 2, 2' — Северского трубного завода; 3, 3' — Павлодарского трубопрокатного завода; 4, 4' — Таганрогского металлургического завода; 1—4 — диаметр заготовки 325 мм; 1 '—4' — диаметр заготовки 300 мм
Для выбранной гильзы (DTDxST = 350x50 мм) диаметр заготовки изменили с 325 до 300 мм и провели расчет на модели (угол подачи 10 град.).
После уменьшения диаметра заготовки (см. рис. 2, кривые 1'—4') есть небольшое снижение числа циклов до носка оправки, что положительно сказывается на процессе прошивки и уменьшает вероятность вскрытия полости перед носком оправки. Накопленная степень деформации сдвига существенно не изменилась, по-прежнему наибольшая проработка структуры по всей длине очага деформации наблюдается на стане Северского трубного завода.
В качестве меры по совершенствованию режимов прошивки на рассматриваемых станах можно рекомендовать (если это осуществимо в технологическом процессе) изменение углов конусности и подачи, использование более длинных оправок, получение заданных размеров гильз из заготовки меньшего диаметра заготовок, применение повышенных обжатий в пережиме валков.
Заключение
Проведено сравнение четырех современных промышленных прошивных станов для производства труб большого диаметра на заводских режимах, используемых для получения «массовых» размеров труб и на «выровненном» режиме с одинаковыми для всех четырех станов размерами заготовки-гильзы.
Выявлено, что на стане Северского трубного завода на сравниваемых режимах наблюдается оптимальная проработка структуры по длине очага деформации и, возможно, будет наблюдаться минимальное число дефектов.
Предложены рекомендации по настройке станов с целью уменьшения числа циклов перед носком оправки и увеличения числа шагов по итогу для повышения проработки структуры непрерывнолитых заготовок из углеродистых сталей.
Библиографический список
- 1.Данилов Ф. А., Глейберг А. 3., Балакин В. Г. Производство стальных труб горячей прокаткой. — М.: Металлургиздат, 1954. — 597 с.
- 2. Матвеев Б. Н., Голубчик Р. М. Новые исследования процесса прошивки заготовок в косовалковых станах // Сталь. 2000. № 9. С. 53-58.
- 3. Голубчик Р. М., Клемперт Е. Д., Меркулов Д. В., Титова С. В. Новая методика расчета параметров на-
- стройки прошивных косовалковых станов // Производство проката. 2001. № 8. С. 20-23.
- 4. Golubchik R. М., Lebedev А. V. New methods piercing mills setting relaring to the cyclic forming of hollows. History and future of seemless steel tubes (7th International Conference)/ Karlovy Vary, 1990, November, p. 1/8-1/17.
- 5. Голубчик P. M., Меркулов Д. В., Клемперт Е. Д. Диаметр прошиваемой заготовки и качество труб // Сталь. 2006. № 4. С. 56-57.
Московский энергетический институт, Россия