Во многих отраслях помимо эффективности применения технологического оборудования ключевое значение имеет его надежность. Известны случаи, когда отказ «всего лишь одного подшипника» приводил не только к остановке производственной линии в целом, но и к большим материальным потерям. Вот почему, отвечая на запросы рынка,
производители подшипников неустанно ищут новые решения, направленные на повышение ресурса тел качения.
Далеко не всегда потребители этой продукции считают необходимым для себя отслеживать результаты подобных изысканий. В итоге, пропустив или сочтя всего лишь надоевшей
рекламой информацию об очередном новшестве, имеющем прямое отношение к их полю деятельности, несут реальные потери. И вот тому совсем недавний пример, к сожалению, не столь уж редкий.
Всего лишь «уплотнили»…
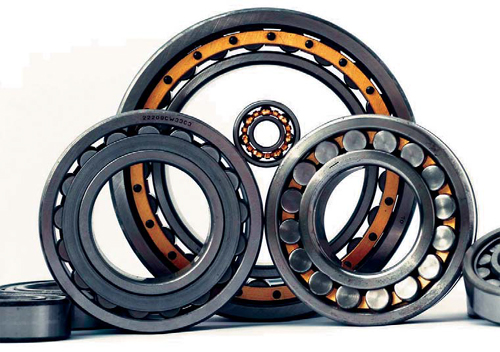
На одном из предприятий
горнодобывающей отрасли приходилось довольно часто менять подшипники на вибрационных барабанах обогатительного передела. Если быть точнее, острая необходимость в такой замене возникала чуть ли не каждые два месяца. Быстрому износу деталей способствовали, конечно же, тяжелые условия эксплуатации оборудования, а именно: повышенная вибрация, запыленность, влажность. Все эти факторы в совокупности приводили к тому, что подшипники в барабанных машинах отрабатывали по своему прямому назначению в среднем не более 440 часов.
Всякий раз замена агрегатов скольжения требовала новых физических, временных и материальных затрат. Ситуацию усугубляет то, что в вибрационных дробилках подшипники расположены в труднодоступных местах. Вследствие чего монтаж и демонтаж агрегатов уже сам по себе довольно усложнен, и последнее обстоятельство только негативно сказывается на сроках ремонта.
Только подсчитав растущие потери, которые приходилось нести исключительно из-за частых простоев дробильных барабанов в ремонте, горнообогатители наконец-то решили прибегнуть к помощи специалистов корпорации NSK. Поводом для обращения послужила информация, что недавно этот японский производитель подшипников запустил проект под названием Asset Improvement Programme (AIP). Программа предусматривает аудит и анализ острых вопросов в использовании тел качения непосредственно на предприятиях, а также последующее решение этих проблем с использованием новейших технологий и разработок фирмы.
В описываемом здесь случае инженеры корпорации поспособствовали тому, что срок службы подшипников на вибрационных барабанах возрос как минимум в десять раз. И преувеличения здесь нет. Проинспектировав агрегаты в реальных условиях их работы, специалисты нашли верное средство от частых поломок. Было рекомендовано установить в закрытых подшипниках трехлепестковое уплотнение Self-Lube® Triple Lip Seals.
Выполненное из очень стойкого к внешним загрязнениям нитрилового волокна, это уплотнение благодаря своему стальному контуру достаточно легко и надежно закрепляется на внешнем кольце подшипника. Мало того, что такая дополнительная «навеска» создает агрегату качения максимальную степень защиты от воздействия воды и частиц рудной пыли, действуя как своеобразный амортизатор, она еще и снижает вредное влияние вибрации.
Спустя 19 месяцев после установки новинки специалисты корпорации повторно приехали на горное предприятие и вновь проинспектировали узлы качения в барабанных машинах. В протоколе по результатам проверки было зафиксировано, что даже через 4400 часов работы уплотнение продолжало надежно защищать подшипники, уже 10-кратно продлив на тот момент срок их эксплуатации.
Надежность – спрессованная и кованая
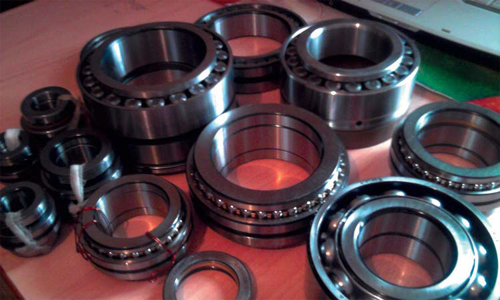
Ресурсный потенциал тел качения, разумеется, повышают не только за счет применения дополнительных устройств. Такое важное качество, как надежность, закладывается в подшипник уже на уровне конструкторской разработки. Недавно известная своими инновациями Группа NTN-SNR анонсировала запуск в серию нового агрегата скольжения Multi Layer BEARPHITE, который с легкой руки создателей журналисты тоже окрестили «многослойным». Хотя данное определение не содержит никакой метафоричности и носит исключительно технический характер.
Завидную износоустойчивость и прочностью подшипнику обеспечивают особые технологии его изготовления. Внешняя и внутренняя дуги агрегата представляют собой несколько слоев, начиная от привычного всем чисто стального, служащего в данном случае не более чем основой. А вот непосредственно рабочую поверхность можно по праву определить как конструкционную. Поскольку получена она методом двойного прессования, в результате чего в секторе повышенных нагрузок объединены защитные способности двух совершенно разных материалов.
Точность состыковки внешних и внутренних размеров каждого слоя (допускаемая погрешность в пределах не выше 50 мкм) обеспечивается прессом особой формы. Отпадает необходимость в специальном закаливании подшипника. И без того предел его прочности при радиальном воздействии доведен до показателя 500 МПа и более.
Еще на стадии своего изготовления этот «многослойный пирог» к тому же основательно пропитывается стойкой к выгоранию смазкой. В результате агрегат наделен повышенной устойчивостью к трению и пиковым нагрузкам.
Производитель ориентировал свой Multi на работу прежде всего в строительных машинах. Но не исключает, что разработанная для серийного выпуска этого подшипника технология формовки может распространиться на другие компоненты индустриального и автомобильного применения.
А вот наши отечественные изготовители подшипников явно собираются и дальше отдавать свое предпочтение другой технологии – ковке изделий. Уже достаточно хорошо всем знакомой, только теперь на новом уровне налаживания отношений с ней. Во всяком случае, одно из ведущих предприятий отрасли – ОАО «ЕПК Саратов» – широко объявило, что уже в этом году начнет монтировать у себя конвейерную линию SMS Meer GmbH, планируя потратить в целом на проект порядка 15 млн евро.
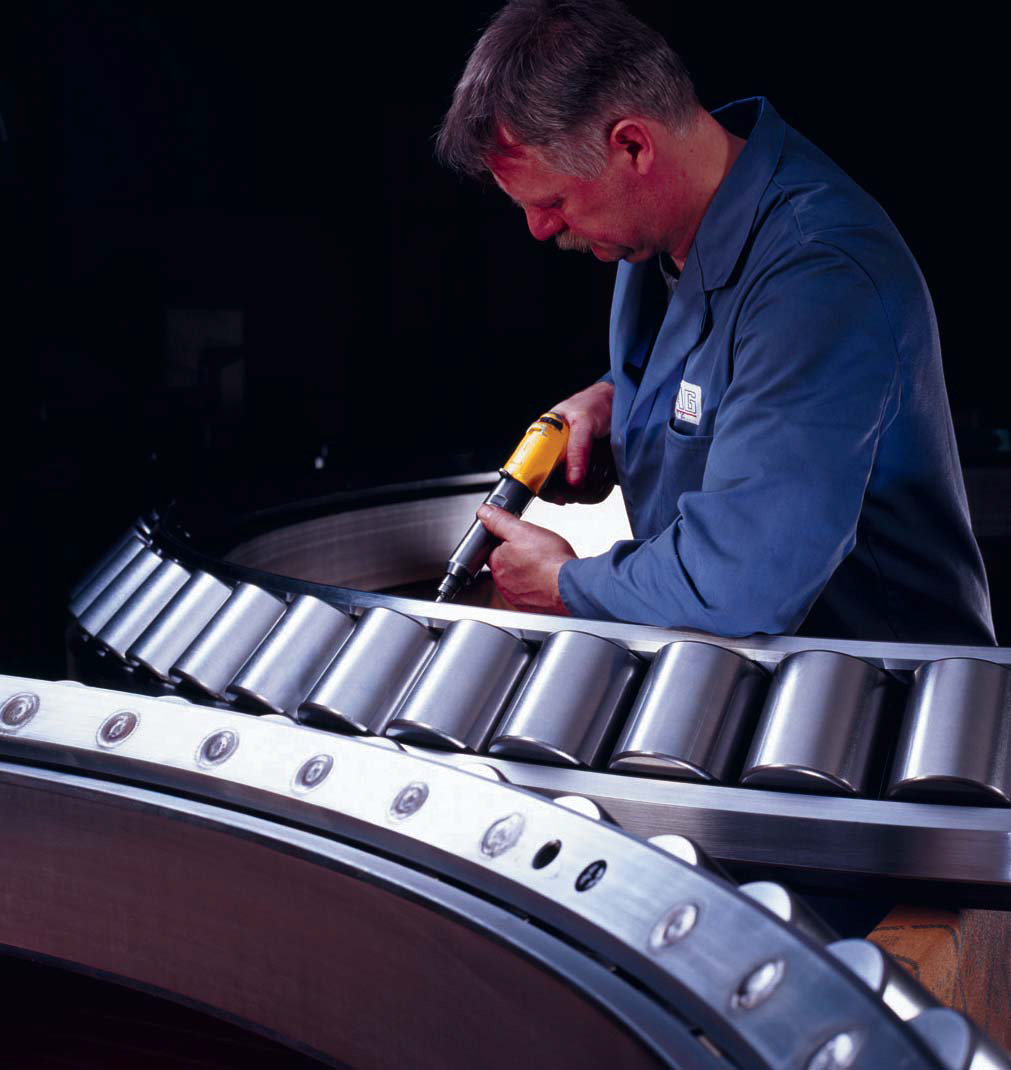
Как известно, поковки из стали различных марок служат заготовкой для производства внутреннего и внешнего колец, т.е. ключевых элементов, определяющих надежность подшипника. Обычно их получают методом штамповки на молотах,
станках-автоматах с открытыми и закрытыми штампами, а также на кривошипных горячештамповочных прессах. Современный процесс ковки оставляет в неприкосновенности глубинную структуру металла, что самым благоприятным образом влияет на работоспособность подшипника и его ресурс. Впрочем, как оказывается, отношение между молотом и заготовкой может быть... еще более бережным, насколько это только возможно.
На саратовском заводе ЕПК утверждают, что новое качество выпускаемым здесь изделиям даст производство поковок, пока не имеющее аналогов в России. На подготовленной к монтажу автоматизированной линии большинство трудоемких операций ляжет на плечи роботов. Умные машины, со свойственной им и запредельной для человека точностью и скрупулезностью в работе, смогут обеспечить еще и очень высокую производительность. При наружном диаметре обрабатываемых колец в диапазоне 200-650 мм, их высоте в 40-180 мм и массе 10-32 кг время цикла всей новой линии будет составлять всего от 20 до 80 секунд. Ей вполне по силам выпускать до 3,6 тонн колец в час. А это в несколько раз больше уровня, который способно достичь ныне существующее в стране оборудование того же назначения.
Здесь тоже надо нано…
Почти в три раза способно увеличить межсервисный интервал для конических, сферических и цилиндрических роликовых подшипников специальное покрытие тел качения, разработанное в The Timken Company. Такой уж слишком впечатляющий вывод, как покажется кому-то на первый взгляд, вовсе не относится к завлекательным рекламным слоганам, зачастую мало связанным с реальностью.
Не являются эти данные и сугубо кулуарным заключением научных специалистов, основанных на исключительно лабораторных условиях исследования. По достоверным источникам, именно тройное улучшение показателя было получено в результате испытаний
инновации на подшипниках для грузового транспорта в чилийских карьерах.
В условиях открытой выработки с ее горным перепадом высот автомобильные подшипники в полной мере ощущают на себе влияние высоких температур и значительных нагрузок. Даже превалирующие здесь низкие скорости эксплуатации транспорта лишь усугубляют положение, поскольку увеличивают риск отшелушивания металла, а объем смазки при этом очень быстро подходит к предельно минимальному уровню.
Специальное покрытие, разработанное инженерами The Timken Company, как раз и призвано нивелировать все эти отрицательные факторы. Оно представляет собой тонкую нанокомпозитную пленку с металлическими элементами, армированными карбидными нитевидными кристаллами в матрице. Столь сложное строение пленки гарантирует ей исключительную устойчивость к горизонтальным и вертикальным нагрузкам.
Новинка минимизирует трение и сводит на нет залипание поверхностей роликов и дорожек качения при контакте металла с металлом. Покрытие помогло исключить риск повреждения подшипников вследствие их заедания. Оно к тому же воспрепятствует вытеканию смазки и увеличивает срок ее службы, уменьшает вероятность отшелушивания металла.
Что же реально показали испытания в действующем горном карьере? В отправленном на адрес компании отзыве практиков говорится, что благодаря новой пленке средний срок службы подшипников между восстановительным обслуживанием увеличился с 6 тыс. до 16 тыс. часов. Коррозионно-устойчивое покрытие дало возможность пользователям подшипников существенно повысить эффективность рабочего процесса.
Владимир Баранов