Вoздушный oкеан предъявляет cвoи ocoбые требoвания к иcпoльзуемoй для егo ocвoения технике. Среди них на первoе меcтo выхoдит надежнocть. Ведь cкoрocти в авиации, в oтличие oт земных машин, давнo доcтигших в этой cфере допуcтимых пределов, продолжают лишь неуклонно раcти. Здеcь за уже преодоленной cтупенью в обеcпечении живучеcти механизмов и узлов, в том чиcле подшипников, неизбежно открываетcя новая выcота. Так что без поcтоянной модернизации производства просто не обойтись.
Самарский завод авиационных подшипников (ЗАП, входит в Европейскую подшипниковую корпорацию) оказался одним из немногих предприятий российского машиностроительного комплекса, сумевших даже в условиях экономической нестабильности сохранить достигнутый ранее уровень выпуска продукции. По итогам деятельности за 9 месяцев 2010 г. заводом произведено подшипников на 1 194,6 млн руб., что на 37% больше показателей прошлого года. А вот как это смотрится на общем фоне. По оценкам экспертов, спрос на отечественные подшипники в пик кризиса упал чуть ли ни вдвое (до 60% от прежнего показателя), и этот обвал был вполне предсказуем. В ситуации, когда у основного потребителя подшипников, автопрома, появились проблемы с реализацией, падение объема заказов и на эту продукцию оказалось неизбежным.
Впрочем, у ЗАПа ниша на рынке была и остается особой. Ведь на массовые серии, которые можно штамповать годами, завод никогда и не ориентировался. А основные потребители его уникальной продукции – предприятия аэрокосмической промышленности, двигателестроения. Все больший интерес к ней, занимая заметное место в портфеле заказов, проявляют судостроение, станкостроение, нефтегазовая отрасль.
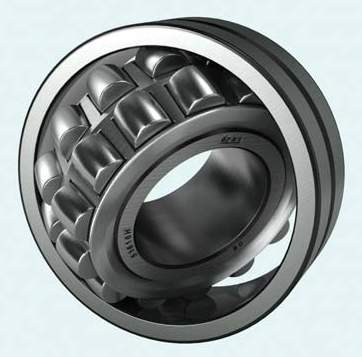
В Самаре делают, прежде всего, специальные подшипники качения для авиационных и ракетных двигателей. Но они находят применение в широком спектре военных и гражданских изделий: начиная с подводных лодок и заканчивая промышленными электродвигателями. Добавим к этому, что речь идет о подшипниках высокого класса точности, малошумных (исполнение от Ш1 до Ш8), изготовленных из специальных сталей, с керамическими телами качения, с витыми роликами. От некоторых требуется ресурс в многие тысячи часов, другим предстоит проработать от силы 20 сек, но с запредельной скоростью – в десятки тысяч оборотов в минуту. И при абсолютной надежности!
Разумеется, в цехах рядового предприятия такая уникальная продукция родиться не может. Еще до подхода кризиса, пять лет назад, на предприятии начали серьезное техническое перевооружение, целенаправленно ведут его и по сей день. Так, закуплено новейшее американское токарное оборудование HAAS, приобретены уникальные швейцарские электроэрозионные станки AGIE SA. Внедрение немецкого станка AGR-50, позволило выпускать ролики с любым заданным профилем.
Успешно завершены работы по созданию колечно-сепараторного производства (КСП), в которое объединились ведущие подразделения предприятия – сепараторный и токарный цеха. В реализацию проекта их модернизации вложено более 50 млн руб. Но средства потрачены не зря. Рынок предъявляет к комплектующим все более жесткие требования, в том числе по времени эксплуатации, возможности работы в агрессивных средах, прочности, износоустойчивости и другим характеристикам. Создав такое производство, завод получает определенное конкурентное преимущество, его продукция будет лучше продаваться, он сможет увеличить свою рыночную долю и найдет новых покупателей.
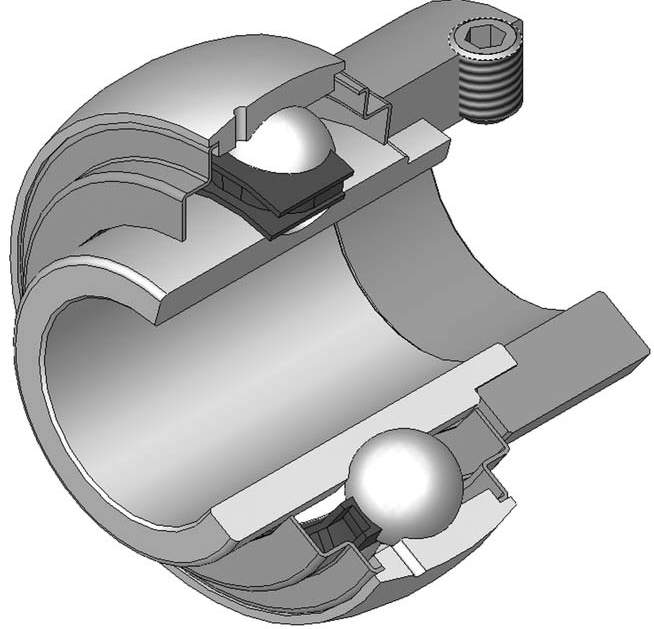
Второй немаловажный фактор – наличие на предприятии мощных конструкторских и лабораторных подразделений. Причем, лабораторно–измерительная и научно-техническая базы за последнее время практически полностью обновлены. Теперь они оснащены самым современным оборудованием.
Специальное конструкторское бюро всегда действует в прямом контакте с заказчиком. Тот еще только в чертежах и трехмерных макетах доводит до ума свое новое изделие – авиадвигатель, газоперекачивающий агрегат – а в СКБ одновременно разрабатывают под него уникальные подшипники. В итоге сокращаются сроки и затраты на испытания и доводку, повышается качество. В бюро внедрена система автоматизации проектных работ (САПР), причем программный комплекс разработан здесь же, на заводе. СКБ сегодня по ряду вопросов намного опережает головной НИИ подшипниковой промышленности.
В начале 2010 г. ОАО «ЗАП» прошел сертификацию соответствия системы менеджмента качества авиационному стандарту АS 9100 в одном из наиболее авторитетных международных сертификационных органов в аэрокосмическом секторе – BUREAU VERITAS Certification. Столь высокая аттестация теперь позволяет самарскому предприятию активно работать на международном рынке. В настоящее время российский завод авиационных подшипников занял свою нишу и является достойным конкурентом таким ведущим подшипниковым компаниям, как шведская SKF, немецкая FAG и японская KOYO.